Maestranza
Matière plastique
Une matière plastique (le plastique en langage courant) est un polymère généralement mélangé à des additifs, colorants, charges (miscibles ou non dans la matrice polymère). Il en existe une large gamme ; moulés par injections, extrudés, étiré en film, généralement façonné à chaud et sous pression, pour aboutir à un semi-produit ou à un objet, y compris fils et fibres (tissus), mastics, revêtements , etc.. Il est utilisé dans presque tous les secteur d'activité. Certains ont des propriétés jamais auparavant réunies, par exemple la transparence et la résistance aux chocs.
Avec environ 400 millions de t/an (en 2022), quantité susceptible de doubler avant 2040, à 90 % issus d'hydrocarbures fossiles il est devenu omniprésent. Et seul environ 9 % du plastique est recyclé (12 % incinérés et le reste mis en décharge ou perdu dans la nature1, peu à peu dégradé en microplastiques et en nanoplastiques), ce qui fait du déchet plastique un problème préoccupant. En mars 2022, les dirigeants mondiaux et les ministres de l'environnement ont entamé des négociations pour un premier traité international (juridiquement contraignant) au monde visant à éliminer la pollution plastique1.
Le mot « plastique » dérive du latin plasticus, lui-même issu du grec ancien πλαστικός (plastikós, « relatif au modelage »), dérivé du verbe πλάσσειν (plássein, « mouler, former ») dont dérive aussi le mot plasma.
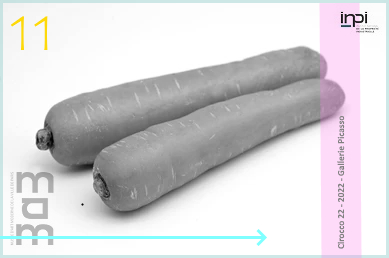
Les premiers plastiques industriels très résistants ont été produits à partir du lait. La Bakélite a connu un immense succès à partir des années 1920 ; ici sous forme de face avant d'un poste de radio. La caséine du lait a servi d'agent plastifiant en peinture dès le Moyen Âge et peut-être bien plus tôt.
Si l'on peut faire remonter l'histoire des matières plastiques à l'Antiquité, c'est surtout à partir de la fin du xixe siècle que leur utilisation se développe avec la mise au point de plastiques synthétiques. Des centaines de chercheurs et de bricoleurs de génie sont à l'origine de cet essor. Les premiers plastiques, artificiels, résultaient de la transformation chimique de polymères naturels tels la cellulose et la caséine (le squelette macromoléculaire étant préservé lors de cette transformation). La première matière plastique industrielle basée sur un polymère synthétique est la Bakélite.
L'histoire des matières plastiques remonte à l'Égypte antique :
- au xve siècle av. J.-C., les Égyptiens employaient des colles à base de gélatine, caséine ou albumine. Ils utilisaient de la gélatine d'os pour le collage du bois. Un document daté de 1470 av. J.-C. décrit la fabrication de la colle d'os dans la construction du mobilier2,3 ;
- fin du xve siècle : Christophe Colomb apporte des plants de caoutchouc appelés Cao (bois) tchu (qui pleure) par les Amérindiens[réf. nécessaire] ;
- 1736 : les naturalistes français Charles Marie de La Condamine et François Fresneau de La Gataudière découvrent le caoutchouc naturel dans le bassin amazonien un peu par hasard ;
- 1835 : Henri Victor Regnault découvre par accident la réaction de polymérisation du chlorure de vinyle ;
- 1839 : l'Américain Charles Goodyear découvre par sérendipité le procédé de vulcanisation du caoutchouc naturel par le soufre ;
- 1862 : l'Anglais Alexander Parkes présente la Parkesine (issue de la cellulose), l'un des plus anciens polymères artificiels, lors de l'Exposition universelle de Londres. Cette découverte est à la base de l'industrie plastique moderne ;
- 1870 : John Wesley Hyatt invente le celluloïd (utilisé dans les balles de tennis de table) qui est considéré comme la première matière plastique artificielle, dont l'origine remonte à 1856. Il est obtenu en plastifiant la nitrocellulose (issue de la nitration de la cellulose du bois) à chaud par le camphre. Il fait suite à un embargo de boules de billard en ivoire pendant la guerre de Sécession aux États-Unis d'Amérique ;
- 1884 : Hilaire de Chardonnet invente la viscose en dissolvant de l'acétate de cellulose dans du chloroforme ;
- 1892 : le scientifique français Auguste Trillat, travaillant sur la caséine du lait, réussit à la durcir en y ajoutant du formol, et obtient la « pierre de lait », un polymère thermodurcissable semi-synthétique. En 1897, la Galalithe est inventée par le scientifique allemand Wilhelm Krische et le chimiste autrichien Adolf Spitteler. Cette matière est plus dure que la corne, plus brillante que l'os et plus soyeuse au toucher que l'ivoire. Bientôt toutes les boules de billard seront en Galalithe. En 1918, commence la fabrication d'articles courants, comme le bouton, le bijou fantaisie, le fume-cigarette ou encore le stylo ;
- 1907 :
- le chimiste belge, naturalisé américain Leo Baekeland découvre les résines formo-phénoliques (sous le nom commercial de Bakélite), les plus anciens polymères synthétiques industriels ; produites par polycondensation du phénol et du formaldéhyde (famille des phénoplastes) ; utilisées à l'origine pour les boîtiers de téléphone, coques de rasoir, poignées de casserole, prises électriques, cendriers, etc. ;
- la même année, le chimiste allemand Fritz Hofmann réalise les premiers caoutchoucs synthétiques en polymérisant des diènes conjugués ;
- 1908 : découverte de la cellophane par le chimiste suisse Jacques E. Brandenberger ;
- 1919 : le chimiste allemand Hermann Staudinger, prix Nobel de chimie en 1953, introduit la notion de macromolécule puis réalise la polymérisation de nombreux monomères éthyléniques. Il peut être considéré comme le père de la science macromoléculaire ;
- 1920 : premières études des réactions phénol-épichlorhydrine par Paul Schlack de la société IG Farben, conduisant aux résines époxyde ;
- 1931 : première fabrication industrielle du polychlorure de vinyle (PVC) ;
- 1932 : après plus de vingt ans de recherches, développement par Otto Röhm et Haas, en collaboration avec la société IG Farben, d'un grand nombre de dérivés polyacryliques, dont le polyméthacrylate de méthyle (PMMA), commercialement connu sous le nom de Plexiglas ; utilisation : feux arrière et de clignotant, certains carters de véhicule, hublots d'avion, fibres optiques, enseignes lumineuses ;
Cageots en matière plastique courante (base PE ou PP).
- 1933 : obtention par polymérisation radicalaire du polyéthylène basse densité (PEBD) (LDPE pour les Anglo-saxons) (densité d~0,92) par les ingénieurs anglais Eric Fawcett et Reginald Gibson de la firme ICI en opérant sous très haute pression à environ 200 °C4. Le polyéthylène ou polyéthène (PE) est la seule polyoléfine qui puisse être obtenue par voie radicalaire ;
- 1935 :
- les polyamides (PA) (connus sous le nom de nylon5) sont sortis des éprouvettes du chimiste américain Wallace Hume Carothers travaillant pour Du Pont de Nemours6. En 1938, la firme annonce officiellement la découverte d'une fibre synthétique « aussi solide que l'acier, aussi fine que la toile d'araignée, et d'un magnifique éclat ». Ce fut le premier plastique technique à haute performance, avec en particulier un coefficient de friction faible.
- Applications : fait ses preuves dans les parachutes des G.I. au moment du Débarquement, puis utilisé dans la confection de bas ; engrenages, cages de roulement à billes, corps de perceuse, têtes de maillet, visserie plastique, semelles de chaussures de football ;
- fabrication industrielle du polystyrène (PS) à Ludwigshafen, suivie d'un rapide développement en Allemagne ;
- 1936 : la société Rhône-Poulenc crée le Rhodoïd, à base d'acétate de cellulose ;
- 1937 : Otto Bayer synthétise les premiers polyuréthanes, aussi appelés polycarbamates7 ; applications : adhésifs, fibres Spandex, « mousses » pour matelas et coussins, sièges d'automobile, etc. ;
- 1938 : Roy Plunkett, un chimiste américain de Du Pont de Nemours, découvre par hasard le polytétrafluoroéthylène [formule moléculaire (-CF2-)n] (PTFE) (principalement connu sous le nom commercial de Téflon ; présent dans le goretex5), un isolant qui offre une excellente résistance chimique à la chaleur (stable jusqu'à 250 °C en service continu, avec pointes possibles à 300 °C). Isolant étanche, il sert dans l'industrie nucléaire militaire, avant de recouvrir dans les années 1960 les poêles à frire des cuisines (application de son pouvoir antiadhésif). Il sert aussi pour les joints d'étanchéité.
La Seconde Guerre mondiale exacerba les besoins en matières premières :
- 1941 :
- la résine « mélamine-formol », alias Formica, envahit les cuisines. Cette résine très dure fait partie de la famille des aminoplastes. Elle a été développée dans les années 1930 et 40 par des firmes telles American Cyanamid, Ciba et Henkel, mais sans véritable succès commercial. Ses propriétés élevées de résistance à la plupart des produits chimiques, à la chaleur, à la lumière, à l'abrasion et au feu expliquent son succès dans l'immédiat après-guerre. Les aminoplastes sont par ailleurs utilisés comme adhésifs/liants dans l'industrie du bois ;
- les silicones (SI), thermostables dotés de propriétés antiadhésives ; utilisation dans les industries électrique, aéronautique et du biomédical (isolants électriques puis fluides amortisseurs dans les trains d'atterrissage des avions, chirurgie plastique, huiles de moteur, mastics, peintures, cosmétiques, etc.) ;
- découverte du polytéréphtalate d'éthylène (PET, PETE) par John Rex Whinfield et James Tennant Dickson.
Pour couvrir ses besoins, l'Allemagne, rapidement privée de ses ressources en latex naturel, avait produit durant la Première Guerre mondiale du caoutchouc Buna8, un ersatz de cette substance. Ses recherches sur de nouvelles matières se poursuivirent au cours de la Seconde Guerre mondiale (réalisées notamment par IG Farben) et, en 1945, la production de caoutchouc synthétique s'élevait à un million de tonnes.
À partir de la Libération, l'élan scientifique et technologique insufflé à l'industrie par la guerre se poursuivit et de nouvelles matières furent synthétisées, telles les nouveaux polyamides, le poly(carbonate de bisphénol A) et les polyacétals.
Puis les découvertes de nouvelles matières se firent plus rares :
- 1950 : synthèse des premiers copolymères du polystyrène, marquant une nette amélioration des qualités du PS homopolymère (tenue au choc en particulier, température limite d'utilisation, tenue aux solvants organiques) ;
Le polycarbonate : une résine transparente comme le verre, la solidité en plus. Utilisée dans les blindages, elle a équipé le casque des astronautes en 1969 sur la Lune.
- 1953 :
- les chercheurs Bottenbruch, Krimm et Schnell de Bayer AG découvrent le polycarbonate (PC), un polymère très transparent et extrêmement résistant aux chocs. Il a équipé le casque des astronautes pour la mission Apollo 11 en 1969. Utilisation : dans plus de 80 % des visières de casque de moto, CD, biberons incassables, phares d'automobile, profilés de toiture, vitres de cabine téléphonique, vitres pare-balles, châssis d'ordinateurs portables, etc. ;
- le chimiste allemand Karl Ziegler et son équipe découvrent fortuitement un système catalytique permettant la polymérisation linéaire de l'éthylène (ou éthène) sous pression modérée (de l'ordre de 2 à 3 MPa), produisant le polyéthylène haute densité (PEHD, d~0,95) au faible degré de ramification ;
- 1954 : un an plus tard, le chimiste italien Giulio Natta met au point, utilisant les catalyseurs « Ziegler », le polypropylène (ou polypropène) isotactique (PP ou PPi pour le différencier du polypropène syndiotactique de sigle PPs). Ziegler et Natta se partagent le prix Nobel de chimie en 1963 grâce à leurs travaux en science des polymères. Remarque : le PP atactique présente peu d'intérêt économique ;
- 1955 : travaux de la société Phillips Petroleum sur la polymérisation linéaire coordinative sous relativement basse pression de l'éthylène, grâce aux catalyseurs stéréospécifiques, fournissant le PEHD ;
- 1961 : commercialisation de l'Estane (BF Goodrich), un polyuréthane thermoplastique (TPU en anglais). Autre exemple d'élastomère thermoplastique (TPE ou TPR en anglais) : le copolymère séquencé (copolymère bloc) SBS ou poly(styrène-b-butadiène-b-styrène) ;
- 1965 : découverte par les chercheurs Stephanie Kwolek et Herbert Blades de la firme Du Pont de Nemours d'un « super-nylon », le Kevlar, une fibre aramide légère et particulièrement résistante9 :
- à la déchirure et aux chocs : gilets et vitres pare-balles, couches anti-perçage ;
- au feu : casques et vestes des sapeurs-pompiers, gants de cuisine, etc. Son grand succès dans ce domaine est aussi dû à l'interdiction de l'amiante ;
- à la corrosion (voiles, amarres de pétrolier) ;
- dans les années 1990, le terpolymère ABS tend peu à peu à remplacer les résines « mélamine-formol ». C'est une matière plus noble que le polystyrène, très utilisée en habillage d'équipements électroménagers (corps d'aspirateur), pour jouets rigides, enjoliveurs, parfois en emballage (couvercles), en accessoires de salles de bains et dans l'industrie ;
- l'ABS existe aussi en version translucide (M-ABS dit ABS transparent) ;
- il est métallisable par galvanoplastie pour imiter l'aluminium ; utilisation : contenants en cosmétique... ;
- il peut être mélangé avec du polycarbonate pour former un mélange de polymères PC/ABS (noms commerciaux Anjablend A, Bayblend, Pulse) (pièces pour automobiles). Le Noryl est un autre exemple de mélange polymère-polymère ;
- 2000 : pour le développement des polymères conducteurs intrinsèques, les chercheurs Alan Heeger, Alan MacDiarmid et Hideki Shirakawa sont récompensés par le prix Nobel de chimie.
Les plastiques armés (matériaux composites) [typiquement les résines polyesters et époxyde renforcées fibres de verre (verre : d~2,5)], plus légers à résistance égale que l'acier ou l'aluminium, et insensibles à la corrosion, sont des matériaux non traditionnels. Certains types sont de plus en plus utilisés dans le secteur aéronautique10.
De nouveaux plastiques plus respectueux de l'environnement (recyclage et biodégradabilité améliorés), moins dépendants du pétrole (réduction de coût), thermostables, plus transparents, incassables, ininflammables ou originaux sont en voie de développement.
Elles varient beaucoup selon les types de plastique dont le spectre propriétés des matériaux plastiques ne cessent de s'améliorer.
On constate l'emploi grandissant de pièces en matières plastiques à la place de pièces métalliques, souvent plus onéreuses, plus sensibles à la corrosion, ou plus lourdes. Certaines caractéristiques techniques diffèrent notablement de celles des métaux :
- la densité des matières plastiques non expansées est nettement plus faible que celle des métaux (hors magnésium) : de 0,83 (cas du poly-4-méthyl-pentène-1 désigné par PMP) à 2,15 (PTFE), avec 1,2 comme valeur moyenne. La densité d'un polymère est directement fonction du taux de cristallinité. Par ailleurs, la rigidité et la résistance mécanique augmentent avec ce taux ;
- température de transformation plus basse : couramment comprise entre 100 °C (le PS est facile à travailler : extrudable dès 85 °C) et 300 °C (le PC est injecté vers 300 °C). Les bioplastiques sont transformés de 160 à 200 °C, contre environ 220 °C pour des compounds ordinaires équivalents ;
- élasticité plus élevée (jusqu'à 800 % d'allongement à la rupture pour le PEHD) ;
- thermostabilité des polymères thermoplastiques nettement inférieure à celle des métaux. Rares sont les plastiques résistant à plus de 250 °C pendant de longues périodes dans l'air. Des modifications structurales, particulièrement parmi les matières thermoplastiques, permettent d'élargir le domaine thermique d'utilisation vers les basses ou hautes températures ;
- module d'élasticité plus faible (le module du PEBD est peu élevé : E~200 MPa ; à l'opposé, les aminoplastes présentent un module très élevé). Une incorporation croissante de fibres augmente le module d'élasticité et la contrainte à la rupture (ténacité) du composite. La dilatation thermique des matériaux est inversement proportionnelle à leur module de traction. Le coefficient de dilatation des polymères thermoplastiques est supérieur à celui des métaux ;
- tenue (ou résistance) aux agents chimiques : en règle générale, les polymères résistent aux acides et aux bases [grande inertie chimique du PTFE et du PE (en raison de sa structure paraffinique)]. Ils sont cependant sensibles aux solvants (bonne tenue du PTFE, PBT et PA-6,6) ;
- les polymères ont un comportement viscoélastique. En effet, ils démontrent simultanément des propriétés élastiques et un caractère visqueux. Dans ce dernier cas, la matière s'écoule en réponse à une contrainte ;
- certains plastiques sont des amortissants vibratoires ; exemples : ABS, copolymère bloc SIS [ou poly(styrène-b-isoprène-b-styrène)] ; intérêt en vibroacoustique ;
- la plupart des polymères thermoplastiques amorphes non chargés (et non colorés...) sont transparents (PMMA, PC, PS « cristal », etc.) ;
- certains plastiques manifestent une grande résistance à l'impact (PC, PET, PMMA, etc.) ;
- certains sont résistants à l'abrasion (PTFE, PVC rigide, polyamides, PET, aminoplastes, etc.). Le PTFE possède un coefficient de friction particulièrement faible qui lui permet d'être un lubrifiant solide ;
- des déchets plastiques très stables peuvent rester des siècles durant dans l'environnement ; ils peuvent cheminer dans des organismes et ceux qui se fixent ont un effet inconnu.
Les matrices organiques sont des isolants thermiques et électriques, ainsi que les fibres de renfort (sauf fibres de carbone)11 :
- la conductivité thermique des polymères est environ cent fois plus faible que celle des métaux ; ainsi, beaucoup de matières plastiques, en particulier les mousses, sont utilisées comme isolants ;
- conductivité électrique très faible ; les plastiques servent traditionnellement pour l'isolation de fils et câbles électriques (PTFE, PEHD).
La matière de base (la résine) est un polymère16. Les résines des matières plastiques sont issues de produits intermédiaires (éthylène, propylène, acétylène, benzène, etc.) dont les matières premières sont le pétrole (notamment grâce au procédé de vapocraquage du naphta), le gaz naturel17 et le charbon.
Un polymère est une substance composée de macromolécules. Une chaîne polymère est constituée d'un grand nombre d'unités monomères. La viscosité et la résistance mécanique d'un polymère augmentent avec le degré de polymérisation (DP ou n) ; ce dernier définit la longueur des chaînes18.
Si le degré de polymérisation est supérieur à 3 000, le produit sera une matière plastique ; le DP peut atteindre six millions.
Les matières plastiques sont synthétisées par polymérisation de monomères ou de (pré-) polymères :
- les polymères monodimensionnels (linéaires ou ramifiés) résultent de la polymérisation de monomères bivalents ;
- les polymères tridimensionnels sont formés par polymérisation de monomères dont la valence moyenne est supérieure à deux, ou par réticulation (par voie chimique ou physique) de polymères linéaires.
La polymérisation est un processus important dans l'industrie chimique car les polymères en résultant doivent présenter les propriétés souhaitées, notamment, la durabilité, l'inertie chimique vis-à-vis de nombreux produits, l'élasticité, la transparence et les résistances mécanique et thermique.
Il existe deux catégories de polymérisations :
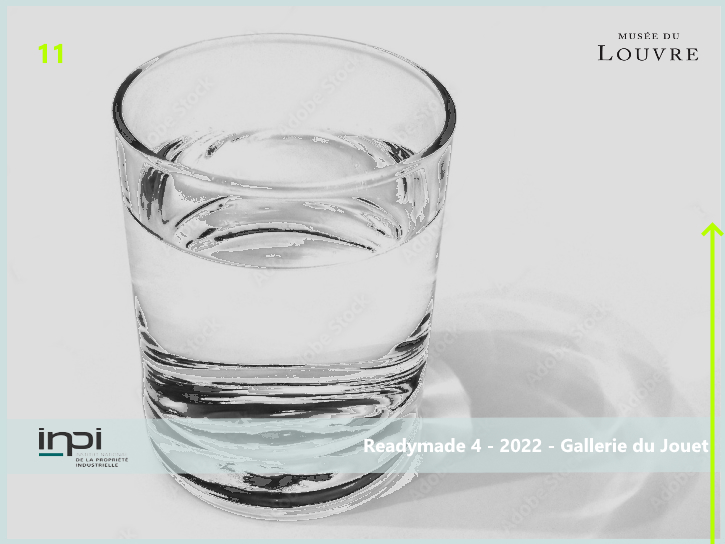
- les polymérisations par étapes, faisant appel à des polycondensations (conduisant par exemple aux polyamides ; la réaction se fait par élimination de molécules simples, surtout l'eau) ou à des polyadditions (pour produire par exemple les polyuréthanes). Les polymères obtenus contiennent souvent des hétéroatomes caténaires, tels les polyamides avec l'atome d'azote ;
- les polymérisations en chaîne. Suivant le type de centre actif, on distingue les polymérisations radicalaires, cationiques, anioniques ou coordinatives (dans ce quatrième cas, le centre actif propageant est un complexe de coordination entre le monomère et un atome de métal de transition tel le titane ou le zirconium). Cette seconde catégorie concerne essentiellement des monomères vinyliques qui conduisent à des polymères constitués d'enchaînements -C-C-.
Pour améliorer certaines propriétés, les matières plastiques du commerce sont parfois constituées d'une résine de base modifiée par une autre résine ou un élastomère (intérêt de la copolymérisation).
Il n'existe pas de macromolécules bidimensionnelles préparées par synthèse.
Il existe quatre procédés de préparation des polymères : polymérisation en masse, en solution, en suspension et en émulsion. Exemples : les polymères thermoplastiques PE, PVC et PS peuvent être synthétisés par ces quatre méthodes de polymérisation. La copolymérisation fournissant l'ABS s'effectue le plus souvent par le procédé en émulsion aqueuse, grâce à la formation de micelles.
Elle joue un rôle important. Les charges, plastifiants et additifs sont incorporés et dispersés dans la matrice de la résine pour en améliorer les caractéristiques (e x: résistance thermique, au feu, chimique, aux chocs, aux U.V ou au vieillissement, masse volumique, couleur, etc.) ou sa mise en œuvre (souplesse...)19.
Pour les usages courant, alimentaire surtout, la formulation doit être non toxique. Une fiche de données de sécurité (FDS) de la préparation doit être disponible pour tous.
Production de granulés (compoundage, ou compounding en anglais) à partir du formulat (polymère formulé) homogène, au moyen d'un malaxeur-extrudeur et d'une extrudeuse. Les granulés seront utilisés, par exemple, pour le moulage par injection.
On distingue (liste non exhaustive) :
- la (les) résine(s) de base : source de la cohésion du matériau ;
- les charges, qui diminuent le coût de la pièce et/ou apportent des propriétés spécifiques, souvent d'autant mieux que leur granulométrie est fine ; avec jusqu'à plus de 100 % d'incorporation en masse dans le matériau polymère pour certains plastisols.
On distingue :
- les charges minérales (poudres en général) : carbonate de calcium naturel20, silices naturelles, silice synthétique (amorphe, agent thixotropique), talc, argile, kaolin, noir de carbone, graphite, barite (d~4,4), ferrite de baryum, etc.,
- les charges organiques ; ex : farine de bois (faible coût) ou d'écorce de fruits, pâte de cellulose, amidon (améliore la biodégradabilité), poudre élastomère (antichoc), etc. ;
- charges métalliques : elles améliorent la résistance aux UV ou peuvent rendre la matrice organique partiellement conductrice (ajout de poudres ou paillettes d'aluminium, cuivre, zinc, plomb , etc.) ;
- les charges renforçantes fibreuses, améliorant les caractéristiques mécaniques, la tenue thermique et la stabilité dimensionnelle du composite (diminution du retrait) (fibre de verre, mica, etc.). L'amiante, en raison des risques pour la santé, n'est plus utilisé ;
- charges renforçantes non-fibreuses (« microbilles » de verre creuses en général), allégeant la résine ainsi chargée, la rendant plus rigide, plus isolante, plus résistante à la compression.
- nouvelles applications :
- argile nanométrique (très fine), incorporée jusqu'à 5 % (pour nanocomposites et emballages de bouteilles),
- céréales, (jusqu'à 50 % d'incorporation pour améliorer la recyclabilité[réf. nécessaire]),
- lin : pour augmenter la dureté du polypropylène... ;
- le(s) plastifiant(s) : diluant(s) peu volatil(s) de faible masse molaire, à l'état solide, ou à l'état liquide (plus ou moins visqueux) ; ils rendent en particulier le composé obtenu plus flexible, plus résilient et diminuent la température de transition vitreuse et la température de mise en œuvre ; ajouté(s) en proportion variable (d'une faible proportion jusqu'à 50 % d'incorporation dans certains plastisols) (phtalates, adipates, sébaçates, phosphates, polyesters, etc.) ;
- additifs.
Généralement incorporés en faible proportion (mais parfois jusqu'à 50 % du poids de la résine) ils améliorent ou créent certaines propriétés des plastiques.
Beaucoup n'ont pas fait l'objet d'une évaluation complète de sécurité en termes de toxicologie ou d'écotoxicologie et ils deviennent préoccupants car ils sont souvent écotoxiques et libérés en quantité croissante par les plastiques qui se dégradent, notamment en mer dans le contexte d'une large contamination du milieu marin par les plastiques, croissante depuis les années 1950.
Faute de réglementation internationale, et dans l'attente de l'application du règlement REACH, ils sont essentiellement autorisés et contrôlés au niveau national. En Europe, la liste d'additifs de la Directive 2002/72/EC concernant les matières plastiques et des articles qui entrent en contact avec des produits alimentaires est une liste positive (les produits non listés sont interdits) depuis le 1er janvier 2010. Une liste ancienne est consultable21.
La réticulation (formation d'un réseau tridimensionnel à partir de polymères linéaires) permet la synthèse de polymères tridimensionnels. Elle nécessite des durcisseurs, catalyseurs et/ou accélérateurs22.
Des additifs ignifugeants sont inclus dans les résines de composants électriques ou électroniques23,24.
En 2014, les additifs les plus utilisés sont (par quantité décroissante)25 :
- Les plastifiants : ils représentaient environ 50 % des additifs pour plastiques vendus dans le monde. Les phtalates représentaient 70 % des plus de huit millions de tonnes de plastifiants vendus dans le monde, en 2014 toujours26 ;
- Les retardateurs de flamme : pour réduire ou empêcher les phénomènes de combustion (jusqu'à 10 % d'incorporation) (hydroxyde d'aluminium, phosphonates, etc.) ; indispensables chaque fois que la sécurité est en jeu car la plupart des matières plastiques sont particulièrement inflammables ; ils doivent être stables dans le temps, peu ou pas toxiques27 ;
- Les modificateurs d'impact : ce sont des molécules ou atomes qui rendent le plastique plus résistant au poinçonnement et à la casse, à basse température notamment ;
- Les antioxydants et autres stabilisants : ils retardent la dégradation du polymère : stabilisants au dioxygène (antioxydants ; tels certains phénols à encombrement stérique ou la diphénylamine28 ; pour les ABS, PE, PS, etc.), à l'ozone (antiozonants ; concerne par exemple les polymères issus du butadiène) ;
- Les agents biocides (fongicides et/ou bactéricides en général) : asepsie, pour résister à l'attaque des micro-organismes, en milieu humide ou hospitalier par exemple ;
- Les stabilisants UV (anti-UV) : tels les absorbeurs UV et les désactivateurs29.
Autres additifs :
- stabilisants thermiques : ils facilitent la mise en œuvre (et secondairement pour la résistance à la chaleur en utilisation, par exemple pour les PVC, PMMA, etc.) ;
- agents gonflants : obtenir un produit-mousse (composé cellulaire peu dense, la densité peut atteindre 0,005) ; un gaz peut être libéré par la décomposition chimique de l'agent sous l'action de la chaleur (isolation, sièges et volants d'automobile, etc.) ;
- lubrifiants : faciliter la mise en œuvre en augmentant le glissement (jusqu'à 2 % d'incorporation) (cires, stéarate de calcium, etc.) ;
- promoteurs d'adhésion : améliorer l'adhésion sur le verre, les fibres de verre ou sur un métal (silanes, titanates, composés contenant des groupes polaires, etc.) ;
- agents antistatiques : ils s'opposeront aux dépôts de poussières en rendant le plastique conducteur en surface ; en effet, la plupart des polymères sont de faibles conducteurs électriques ;
- solvants : pour peintures (enduction), adhésifs, etc. ;
- colorants : ce sont des pigments solides insolubles qui sont ajoutés au polymère, tels le noir de carbone, divers oxydes métalliques ou des colorants organiques30 solubles dans le polymère).
Certains de ces additifs sont multifonctions : ainsi, le noir de carbone (ou carbon black) est utilisé depuis très longtemps dans l'industrie des matières plastiques sous forme pulvérulente, à la fois comme pigment, comme stabilisant (à l'oxydation, aux ultraviolets et à la chaleur), comme nanocharge de renforcement des propriétés mécaniques des élastomères et comme conducteur électrique.
On peut classer les polymères en deux types, en fonction de leur comportement à la chaleur : les thermoplastiques (polymères linéaires, ramifiés ou non) et les thermodurcissables [polymères tridimensionnels (réticulés)]31 :
- portés à une température suffisante (au-dessus de leur température de transition vitreuse Tv ou de fusion Tf), les polymères thermoplastiques se trouvent à l'état « fondu » (état fluide ou déformable) et sont donc susceptibles de s'écouler sous l'action d'une contrainte. Cela permet leur mise en forme au moyen des techniques habituelles (thermoformage, extrusion, injection, etc.). L'opération peut se répéter plusieurs fois ;
- les polymères thermodurcissables durcissent (réticulent) lors d'un premier chauffage (ou éventuellement à température ambiante). Dans le domaine des peintures, c'est une propriété très souvent mise à profit. Un apport de chaleur peut déclencher une réaction de polymérisation tridimensionnelle qui crée des pontages entre les chaînes de polymères et durcit de manière irréversible le matériau.
Les polymères thermodurcissables sont souvent rigides et cassants et les polymères thermoplastiques et les élastomères montrent une résistance mécanique médiocre et très affectée par la température.
La structure moléculaire des matériaux polymères solides peut être soit :
- semi-cristallinne ; [présence de zones cristallines (cristallites et sphérolites) et existence d'un intervalle de fusion étroit qui permet une transition rapide de l'état solide ou pâteux à l'état fluide, par élévation de température], à morphologie hétérogène (exemples : PE, PPi, PA, polyesters thermoplastiques, POM [(-CH2-O-)n], PTFE) ;
- amorphe, montrant un ramollissement progressif par élévation de température (PS et ses copolymères, PMMA, PC, PVC32, etc.).
Remarque sur l'influence de la tacticité : un polymère atactique (PMMA, PS, etc.), dont la chaîne macromoléculaire présente une forme géométrique irrégulière, ne peut pas cristalliser, contrairement à un polymère isotactique ou syndiotactique.
Les propriétés thermomécaniques d'un Polmère dépendent de sa structure moléculaire et son « taux de cristallinité ». ainsi, lors de l'injection, un plastique amorphe est plus tolérants [process plus aisé, retrait (shrinkage en anglais) plus faible au refroidissement] qu'un polymère semi-cristallin (qui a une prédisposition à cristalliser), et le retrait de la matière semi-cristalline est plus important que celui de la matière amorphe, car sa structure est plus compacte (le « module de Young » augmente lorsque le taux de cristallites augmente. Inversement, la limite de déformation élastique diminue).
Les propriétés d'un plastique technique sont souvent jugées optimales quand la cristallinité moyenne permet de combiner une résistance mécanique et thermique de la phase cristalline à la résilience de la phase amorphe (pratiquement 50 à 60 %).
La plupart des thermoplastiques ne sont pas utilisés au-dessus de 120 °C, température à laquelle se produit un ramollissement (pour les amorphes) ou une fusion (pour les semi-cristallins), qui supprime les propriétés mécaniques. Les polymères thermoplastiques amorphes sont utilisés en dessous de leur Tv, à l'état vitreux. En principe, les matières thermodurcissables ont une meilleure tenue thermomécanique (à la chaleur, au feu, au fluage, faible retrait, etc.) et chimique que les thermoplastiques. Les meilleurs thermostables sont des thermodurcissables.
Les matériaux plastiques réagissent aux contraintes d'usage par des déformations, changements de couleur et parfois la rupture selon des seuils qui vont définir leurs propriétés d'usage. Connaître, grâce à la résistance des matériaux, les propriétés intrinsèques des plastiques permet de les choisir judicieusement, selon les fonctions qui leur seront assignées et en fonction du degré de recyclabilité ou biodégradabilité qu'on veut leur accorder.
Leurs propriétés mécaniques intrinsèques sont évaluées via des essais comparatifs, normalisés. En général, on utilise les normes ISO, ASTM et DIN, ou des normes « maisons » lorsque les tests sont directement liés aux propriétés d'usage. Ces tests permettent de prédire les propriétés finales des objets finis. Toutefois, certains caractéristiques structurales liées au degré de cristallinité, à l'orientation des chaînes macromoléculaires, ou aux tensions internes résultant des conditions de mise en œuvre et de refroidissement, peuvent aussi influencer les propriétés de l'objet. Ces propriétés sont dites propriétés de transformation.
En résumé, on distingue :
- les propriétés intrinsèques (propres au matériau) ;
- les propriétés de transformation (fonction des méthodes et conditions de mise en œuvre) ;
- les propriétés d'usage (définies par les conditions d'utilisation).
Un grand nombre d'essais mécaniques utilisés pour caractériser les matières plastiques sont inspirées de techniques d'analyse de métaux et autres matériau (bois, ciments...) telles les mesures du module d'élasticité, de la résistance à la traction et de l'allongement à la rupture.
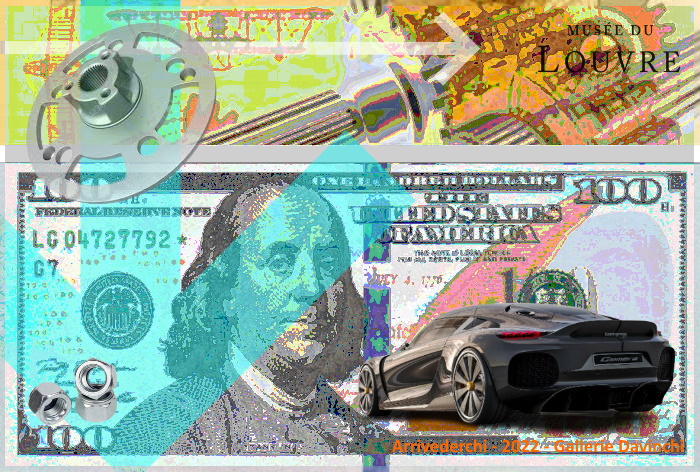
Caractérisation mécanique : courbe contrainte-déformation établie pour un échantillon de trois matériaux-types.
Les analyses mécaniques et rhéologiques sont basées notamment sur des essais de traction, compression, cisaillement, flexion et torsion.
Les équipements d'analyse comprennent les appareils de mesure de l'indice de fluidité à chaud (pour les polymères thermoplastiques) (MFI, Melt flow index en anglais)33, les appareils de traction, les extensomètres, les analyseurs DSC, les viscosimètres (de type rotationnel, cône-plan ou capillaire) (pour les thermoplastiques), les analyseurs DMA (ces deux derniers instruments sont affectés aux mesures dynamiques), les appareils de choc Izod et choc Charpy, etc.
Pour les polymères solides, un simple essai de traction uniaxial permet de mesurer certaines propriétés mécaniques.
Les matériaux se répartissent d'après leur comportement en contrainte-déformation, en trois grandes catégories : rigides (souvent peu ductiles et peu résistants aux chocs), plastiques ou élastomères. Le graphique intitulé « Caractérisation mécanique » obtenu lors d'un essai de traction met en évidence ces trois catégories :
- la courbe A illustre le caractère en contrainte-déformation d'un polymère rigide (module élevé) dont la rupture se produit quasi simultanément à la limite d'élasticité. Le polymère a un comportement fragile (faible allongement à la rupture) ;
- la courbe B montre que le comportement de certains matériaux plastiques est semblable à celui de nombreux matériaux métalliques : la déformation élastique initiale est suivie d'une déformation plastique. Le matériau est tenace (fort allongement à la rupture) ;
- la courbe C indique une déformation élastique dans un large domaine de déformation ; ce comportement mécanique est typique d'un élastomère.
Les matières plastiques ont des propriétés mécaniques influencées par les principaux facteurs suivants :
Influence de la température : courbe établie pour un échantillon de plastique à différentes températures.
- la température ;
- la cohésion des polymères ;
- la modification des propriétés mécaniques moléculaires des polymères ;
- leurs conditions de transformation.
Globalement, le module d'élasticité et l'allongement à la rupture des polymères rigides se déterminent de la même façon que dans le cas des métaux.
La limite d'élasticité Re des polymères plastiques équivaut sur la courbe à la valeur maximale de la contrainte se situant à la fin de la région élastique linéaire. De plus, la résistance à la traction Rm correspond à la contrainte entraînant une rupture ; elle peut prendre une valeur supérieure ou inférieure à Re.
Les propriétés mécaniques des polymères thermoplastiques et des élastomères dépendent fortement de la température (voir le graphique intitulé « Influence de la température »), des contraintes extérieures et du temps d'observation. Une élévation de température fait passer un matériau thermoplastique d'un comportement rigide et fragile à un comportement ductile et tenace.
Plus que tout autre matériau, les plastiques offrent un large choix de techniques de transformation. Les produits initiaux [formulations complètes (nommées aussi matériaux polymères), compounds] se présentent sous forme de granulé, poudre, pastille, pâte ou liquide. Les matières hygroscopiques (PA, ABS, PBT, PMMA, etc.) subissent un préséchage (par étuvage) avant la mise en œuvre afin d'éviter tout défaut lié à l'humidité sur les pièces plastiques.
Les états plastique ou visqueux sont nécessaires pour mettre en œuvre les techniques de mise en forme des matériaux polymères.
Les transformateurs réalisent les objets finis destinés aux utilisateurs à l'aide de matériels et de matières fournies par les producteurs de polymères ou les compoundeurs.
Presse à injecter bimatière alimentée par des granulés thermoplastiques34.
La mise en forme des polymères thermoplastiques diffère de celle des thermodurcissables :
- le moulage par compression à chaud est le moulage-type des polymères thermodurcissables. Il faut éviter la prise en masse (l'atteinte du « point de gel ») de la matière avant que l'opération de moulage soit terminée. Les temps de polymérisation des thermodurcissables limitent les cadences de production de type industriel ;
- le calandrage (passage de la matière entre deux cylindres chauffés), l'extrusion (passage à travers une filière) et le moulage par injection sont les techniques de transformation typiques des polymères thermoplastiques. Ces composés autorisent des temps de cycle plus courts.
Film (à base d'un mélange copolyester-PLA) obtenu par extrusion-gonflage.
On distingue :
- Enduction de supports divers (métaux, tissus, etc.) ;
- Extrusion de cordons, plaques, profilés, tubes35, calandrage, extrusion-calandrage, extrusion-gonflage et extrusion dite cast (obtention de films), coextrusion (films multicouches), extrusion-gainage (câbles) ;
- Injection36, injection assistée eau ou gaz, bimatière ;
- Moulage par soufflage (extrusion-soufflage et injection-soufflage) et rotomoulage : pour créer des corps creux (bouteilles, flacons, jouets, etc.) ;
- Thermoformage, formage sous pression ;
- Moussage (PUR, PS expansé) ;
- Filage à l'état fondu (PP, PET, PA, PE, etc.) ;
- Frittage (du PTFE, vers 370 °C ; du polyéthylène de masse molaire très élevée désigné par UHMWPE en anglais37 ; des PI) ;
Le plastique permet le moulage et le soufflage de formes complexes, en séries industrielles (plasturgie). Les bouteilles en plastique sont ainsi réalisées, à l'aide de techniques très proches de celles utilisées pour les bouteilles en verre.
- Moulage par compression, compression-transfert, coulée, injection : techniques applicables aux thermodurcissables ;
- Procédé RIM (Reaction Injection Molding) (s'appliquant aux résines polyuréthanes thermodurcissables ; la réaction (réticulation) a lieu dans le moule) ;
- Pultrusion, moulage au contact, stratification en continu, moulage à la presse, enroulement filamentaire, injection : fabrication de matériaux composites ;
- Usinage à l'outil ;
- Soudure plastique (par lame chaude, friction, haute fréquence, etc.) ;
- Granulation (broyage des pièces pour recyclage) ;
- Agglomération (ou densification) [récupération, par reformage, de déchets de faibles épaisseurs (films ou équivalents)] ;
- Revêtement de supports à partir de poudre plastique : fluidisation, procédé électrostatique, thermolaquage, pistolage au chalumeau (pour cette dernière technique, une certaine décomposition de la matière est inévitable) ;
- Métallisation : électrolytique, sous vide, argenture (dépôt par réduction du nitrate d'argent) ;
- Pré-traitement superficiel oxydant par effluve électrique ozonisante (procédé corona) avant impression.
Entre 1950 et 2017, selon l'Atlas du plastique de la fondation Heinrich Böll, 9,2 Gt (milliards de tonnes) de matières plastiques ont été produites. Sur plus de 400 Mt (millions de tonnes) produites chaque année dans le monde, contre 2 Mt en 1950, 158 Mt sont utilisées par le secteur de l'emballage. 40 % environ des produits en plastique sont jetés au bout de moins d'un mois49. 51% de tous les plastiques sont produits en Asie, où le plus grand producteur est la Chine50.
La production mondiale de plastiques augmente régulièrement ; 1,5 Mt en 195051, 280 Mt en 201152, 311 millions de tonnes en 201453, 322 millions de tonnes en 201554. La production mondiale de plastiques cumulée depuis 1950 se monte à 8,3 milliards de tonnes (6,3 sont des déchets, dont seuls 9 % ont été recyclés, 12 % ont été incinérés et 79 % accumulés dans des décharges ou dans la nature) et pourrait atteindre 25 milliards de tonnes d'ici à 2050, selon une étude publiée le 19 juillet 2017 dans la revue Science Advances55. Avec une production mondiale de ~54 Mt en 2001, le polyéthylène [(-CH2-)n] est un polymère de synthèse très consommé56. Les plus répandus sont le polypropylène [(-CH2-CH(CH3)-)n], le polyéthylène, le poly(chlorure de vinyle) [(-CH2-CH(Cl)-)n], le polystyrène, le polyuréthane et le poly(téréphtalate d'éthylène) (PET, PETE).
Le PET et le poly(carbonate de bisphénol A) (PC, thermoplastique technique) connaissent une forte progression depuis les années 1990. La production totale du PET était de ~18 Mt en 2001.
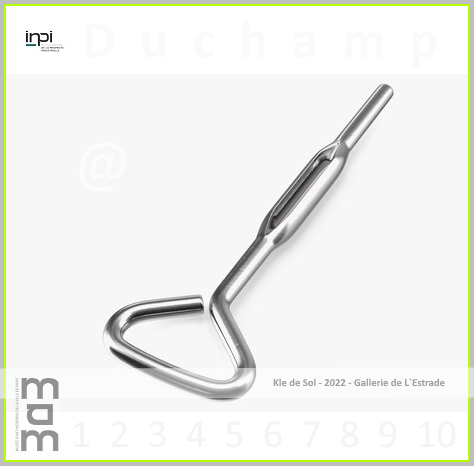
Eucalyptus
Les eucalyptus ou eucalyptus , Eucalyptus L'Hér. (du grec ευκάλυπτος eukályptos, signifiant « bien couvert », faisant référence à la graine dans sa capsule), est un genre d' arbres (et quelques arbustes ) de la famille des Myrtacées . Il en existe environ sept cents espèces , la plupart originaires d' Australie et de Nouvelle-Guinée . Actuellement, ils sont distribués dans une grande partie du monde. Il est considéré comme une espèce exotiqueen Colombie, au Chili, aux États-Unis, en Afrique du Sud et dans certains pays européens. 2
Son utilisation principale est dans les monocultures forestières pour la production de pâte de cellulose pour l' industrie papetière . Dans une moindre mesure, il est utilisé comme combustible, dans l' industrie du bois ou pour obtenir des produits chimiques, en plus de sa valeur ornementale.
Le genre a été décrit par Charles Louis L'Héritier de Brutelle et publié dans Sertum Anglicum , p. 11, pl. 20 , 1789. 34 L' espèce type est Eucalyptus obliqua L'Hér., 1789. Le nom eucalyptus est un mot grec composé de εύ , bon, blond et χαλύπτω , couvrir, couvrir, par l'opercule, étroitement ajusté à l' hypanthe , qui est libéré à l'anthèse.
Les eucalyptus sont des arbres et des plantes médicinales vivaces pyrophytes , érigés. Ils peuvent atteindre plus de 60 m de hauteur, bien que l'on parle de spécimens éteints qui ont atteint 150 m. Chez certains spécimens, l'écorce externe (rhytidome) est brun clair avec une apparence de peau et se détache en bandes laissant des taches grises ou brunâtres sur l'écorce interne plus lisse. 8
Les jeunes feuilles des eucalyptus sont sessiles , ovales, grisâtres et falciformes. Ceux-ci s'allongent et prennent une couleur vert bleuâtre vif à l'âge adulte; 9 contiennent une huile essentielle , à l'odeur balsamique caractéristique, qui est un puissant désinfectant naturel . dix
La plupart des eucalyptus sont intolérants au gel ou tolèrent un gel léger jusqu'à -3°C à -5°C ; les plus résistants au froid sont les eucalyptus dits « des neiges », comme l' Eucalyptus pauciflora , qui est capable de résister au froid et au gel jusqu'à -20 °C. Deux sous-espèces, E. pauciflora subsp. niphophila et E. pauciflora subsp. debenuzevillei , en particulier, sont plus résistantes au froid et peuvent tolérer des hivers assez rigoureux. Certaines autres espèces, en particulier des hauts plateaux et des montagnes du centre de la Tasmanie , telles que Eucalyptus coccifera , Eucalyptus subcrenulata et Eucalyptus gunnii, ont produit des formes extrêmement résistantes au froid et les graines de ces lignées génétiques sont achetées et plantées pour l'ornement dans les régions plus froides du monde.
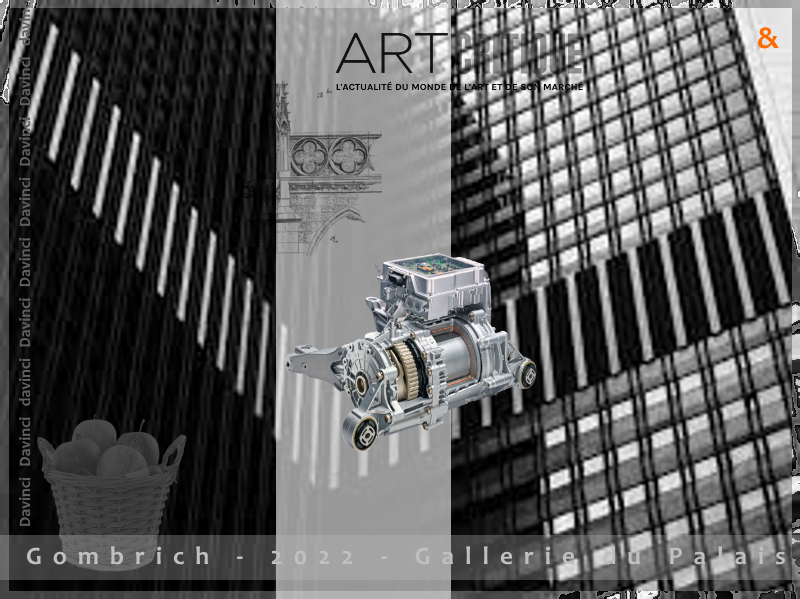
L'expédition de Cook en Australie en 1770 a introduit les eucalyptus dans le reste du monde. Les premières espèces ont été collectées par Sir Joseph Banks , un botaniste de l'expédition, qui les a ensuite introduites dans des endroits tels que la Californie , l'Europe du Sud, l'Afrique, le Moyen-Orient , l'Asie du Sud et l'Amérique du Sud. Les premières utilisations de l'eucalyptus étaient comme brise -vent , car son bois est dur et difficile à scier. 11
L'eucalyptus est un arbre à croissance rapide, dont la racine peut être coupée et repousse. Le principal avantage de ces arbres est leur bois, qui est utilisé pour la menuiserie, le bois de chauffage et la pâte à papier. De plus, son bois est très résistant à la décomposition en raison de sa forte teneur en huile, c'est pourquoi il est utilisé pour les poteaux de clôture. La cellulose peut être extraite pour la production de papier et de biocarburants .
L'eucalyptus est la source la plus courante de fibres courtes pour la fabrication de la pâte de cellulose 12 , utilisée dans divers produits de l'industrie papetière. Depuis les années 1970, environ 80% des cultures forestières d'eucalyptus ont été utilisées à cette fin.
Les types les plus largement utilisés dans la fabrication du papier sont Eucalyptus globulus (dans les zones tempérées) et l'hybride Eucalyptus urophylla x Eucalyptus grandis (dans les tropiques). 16
Selon le type de pâte, ils sont utilisés pour fabriquer des boîtes et des cartons d'emballage, du papier journal, des étiquettes de produits, entre autres utilisations. 1718 La longueur du grain de l' eucalyptus est relativement courte et uniforme avec peu de rugosité par rapport aux autres bois durs couramment utilisés comme bois à pâte. Les fibres sont minces, mais à parois relativement épaisses. Cela permet une formation de papier uniforme et une opacité élevée qui sont importantes pour tous les types de papiers fins. Une faible rugosité est importante pour les papiers couchés de haute qualité . 12 L'eucalyptus convient à de nombreux papiers de soiecar les fibres courtes et fines donnent un nombre élevé de fibres par gramme et la faible rugosité contribue à la douceur. 12
Les premières recherches sur l'utilisation de l'eucalyptus dans la fabrication du papier ont commencé vers les années 1950 . En 1970, l'eucalyptus a été rapidement adopté comme principale matière première pour la pâte de cellulose.
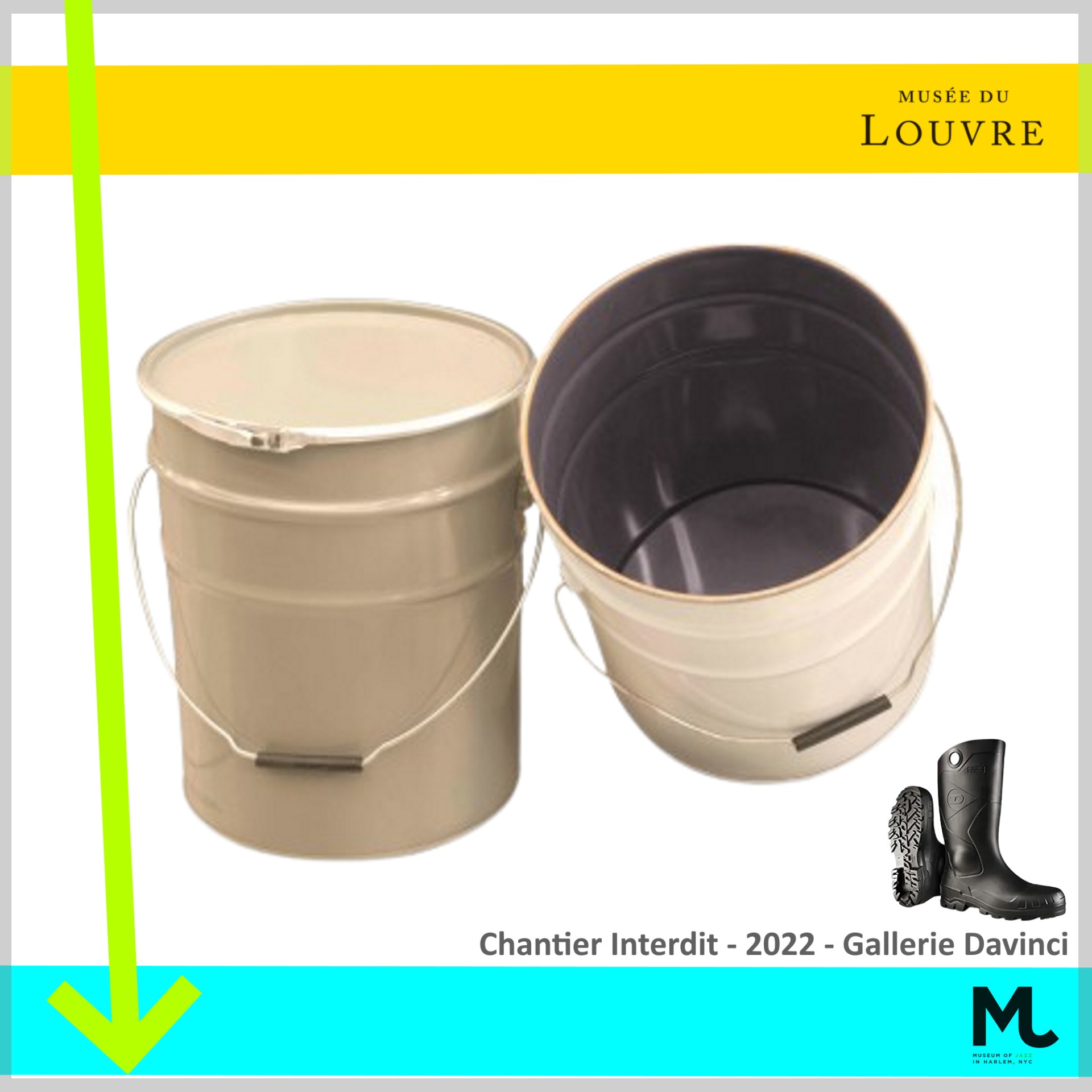
L'huile essentielle de feuilles d'eucalyptus est utilisée comme décongestionnant nasal et pour lutter contre les infections respiratoires. Il est utilisé sous forme de pommade, de pilules, de bonbons inhalés, d'infusions, de sirops ou de vaporisations. L'huile est utilisée par voie topique comme traitement des douleurs musculaires et articulaires, ainsi que pour traiter les boutons de fièvre. Il sert également de répulsif naturel contre les moustiques. 20
Il existe plus de 700 espèces d'eucalyptus et la plupart sont originaires d'Australie. un très petit nombre se trouve dans les régions adjacentes de la Nouvelle-Guinée et de l'Indonésie . L'une des espèces, Eucalyptus deglupta , s'étend jusqu'aux Philippines . Sur les 15 espèces distribuées en dehors de l'Australie, seules neuf sont exclusivement d'origine non australienne. Les espèces d'eucalyptus sont largement cultivées dans le monde tropical et tempéré, y compris les Amériques, l'Europe, l'Afrique, le bassin méditerranéen, le Moyen-Orient, la Chine et le sous-continent indien. Cependant, la gamme dans laquelle de nombreux eucalyptus peuvent être plantés dans la zone tempérée est limitée par leur tolérance limitée au froid. 21
Les plantations forestières d'eucalyptus génèrent des impacts environnementaux, économiques et sociaux. L'eucalyptus produit une acidification du sol et diminue la teneur en argile. 22 Une étude menée dans le nord-est de l'Uruguay a révélé que, par rapport à l' écosystème des prairies , il y avait une perte de matière organique dans le sol et une tendance à la podzolisation . 23 Les plantations intensives sont également une menace pour de nombreux amphibiens et reptiles, dans la mesure où elles impliquent l'altération ou la perte de la végétation indigène et des changements importants dans la dynamique des écosystèmes d'origine. 24
Au Brésil, les monocultures d'eucalyptus génèrent des conflits environnementaux entre les entreprises de production de papier et les communautés indigènes et quilombolas des États d' Espírito Santo et de Bahía .
Les plantes pyrophiles pourraient également être définies comme des pyrophytes (du grec πυρός - pyrós - signifiant « feu » et phyton signifiant « plante »).
Il existe de nombreuses affinités avec lesquelles une espèce végétale peut être positivement liée au feu; la majorité implique d'avoir des adaptations qui signifient qu'ils ont un avantage contre cet événement, qui est généralement lié à la destruction de leurs concurrents non adaptés, avec lesquels ils vivent dans leur phytocénose , avec la libération conséquente de l'espace occupé par ceux-ci , qui une fois transformés en cendres sont utilisés comme nutriments par les pyrophiles. Dans les écosystèmes où des incendies naturels se produisent en raison de leurs caractéristiques climatiques (Méditerranée, continentale , vents violents , orages électriques, etc.) une bonne partie de la végétation présente des caractéristiques qui la rendent pyrophile. Dans les régions où il n'y a pas eu d'incendies naturels, mais du fait de l'action humaine (accidents, attentats ou dans le cadre d'une certaine gestion agricole ou forestière) les incendies sont fréquents, les espèces qui ne les supportent pas finissent par disparaître, leur niche étant occupée par les pyrophiles, à la fois indigènes et exotiques à cet écosystème.
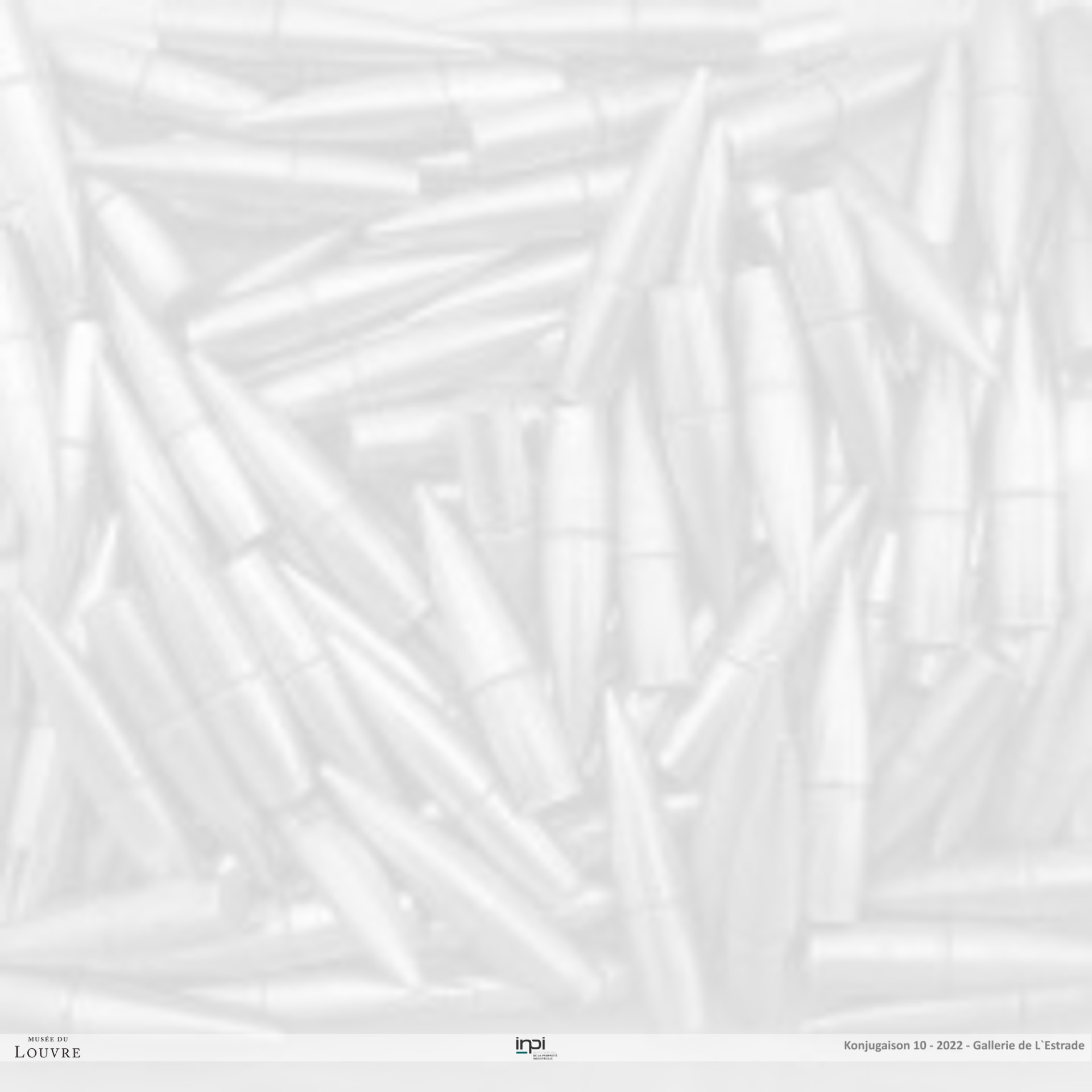
Certains écosystèmes ne peuvent être maintenus que sous une fréquence d'incendie moyenne à élevée. C'est une des séries (succession secondaire) qui font partie d'un cycle de succession , qui, grâce à la périodicité du feu, n'arrive pas à évoluer vers les étapes suivantes.
Certaines plantes supportant le feu sur pied sont utilisées par les producteurs forestiers pour en faire des « pare-feux vivants », qui sont créés sur de longues bandes de largeur variable en plantant de fortes densités de ces essences, ce qui produit l'effet barrière en cas d' incendie , l'empêchant de se propager. s'étendant d'un côté à l'autre de ladite bande, isolant ainsi les cultures forestières, constituées d'espèces à fort intérêt économique mais sensibles au feu.
De nombreuses espèces de palmiers et certaines essences d'arbres peuvent résister à des incendies -non catastrophiques-, qui progressent rapidement et à basse température, libérant les pyrophiles de la concurrence.
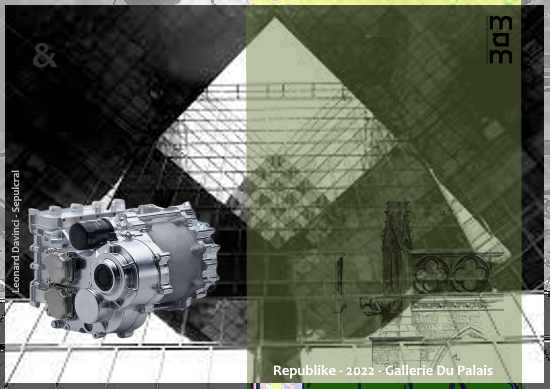
Les adaptations les plus courantes pour résister au feu sont : écorce épaisse avec grande épaisseur de suber , xylopodes puissants , développement de tuniques de cataphylle , germination de bourgeons épicormiques, bourgeons terminaux de branches protégées, etc. Ces adaptations sont courantes chez les espèces qui habitent les formations végétales qui ont évolué sous le facteur de mise en forme des incendies, par exemple, la province phytogéographique du Cerrado . 2 3
Dans certains types de gestion au champ des établissements d'élevage , les zones sont travaillées de manière sophistiquée, générant des perturbations pyrogènes de haute fréquence et de faible intensité, entretenant ces feux dirigés à flammes basses, qui passent rapidement, ne brûlant que les parties sèches des graminées, et sans atteindre des niveaux thermiques trop élevés, ce qui signifie que le feu ne détruit pas les branches des arbres non pyrophiles, pas même leurs troncs. Cette gestion évite une accumulation importante de matières inflammables ; empêchant ainsi la survenue d'incendies catastrophiques, qui élimineraient les plantes ligneuses indigènes, qui fournissent au bétail des fruits et de l'ombre estivale. Bien qu'ils ne soient pas affectés par les flammes, ces espèces d'arbres ne doivent pas être classées comme pyrophiles.
Le yatay est un palmier de savane qui pousse dans les zones où la végétation climacique est la forêt semi-érophile. Son association monospécifique, la palmeraie, ne peut se développer qu'en générant des feux doux et en les répétant à intervalles réguliers. Ce qui se passe, c'est que ce palmier est une plante pionnière, il ne peut donc se développer que s'il a du soleil dès son jeune âge. Lorsqu'une destruction de la masse forestière naturelle se produit, les spécimens les plus anciens qui s'y trouvent (c'est une espèce qui peut vivre plus de 800 ans et atteindre environ 18 mètres de hauteur) répandent leurs graines, qui une fois libérées de l'ombre perpétuelle projetée par la forêt commencent grandir, mais aussi les chilcas ( Baccharis sp. etEupatorium bunifolium ), des arbustes qui forment des communautés denses qui finiront par étouffer les palmiers encore petits. Deux scénarios peuvent se produire ici. Dans les premiers incendies ne se produisent pas, donc la plupart des petits palmiers meurent, avec seulement quelques survivants, qui seront ceux qui remplaceront les palmiers centenaires. Le chilcal est lentement colonisé par des espèces d'arbres de la forêt xérique, qui finiront par former une canopée dense et sombre, ce qui empêchera le yatay de se développer. Dans le deuxième scénario, les incendies continuent de se produire toutes les quelques années, pour lesquels les chilcals et les arbres xérophiles sont incapables de coloniser la zone. Les petits palmiers, qui résistent au feu, parviennent à pousser sans concurrence, générant en quelques décennies une dense palmeraie-herbier, paysage anthropique possible.
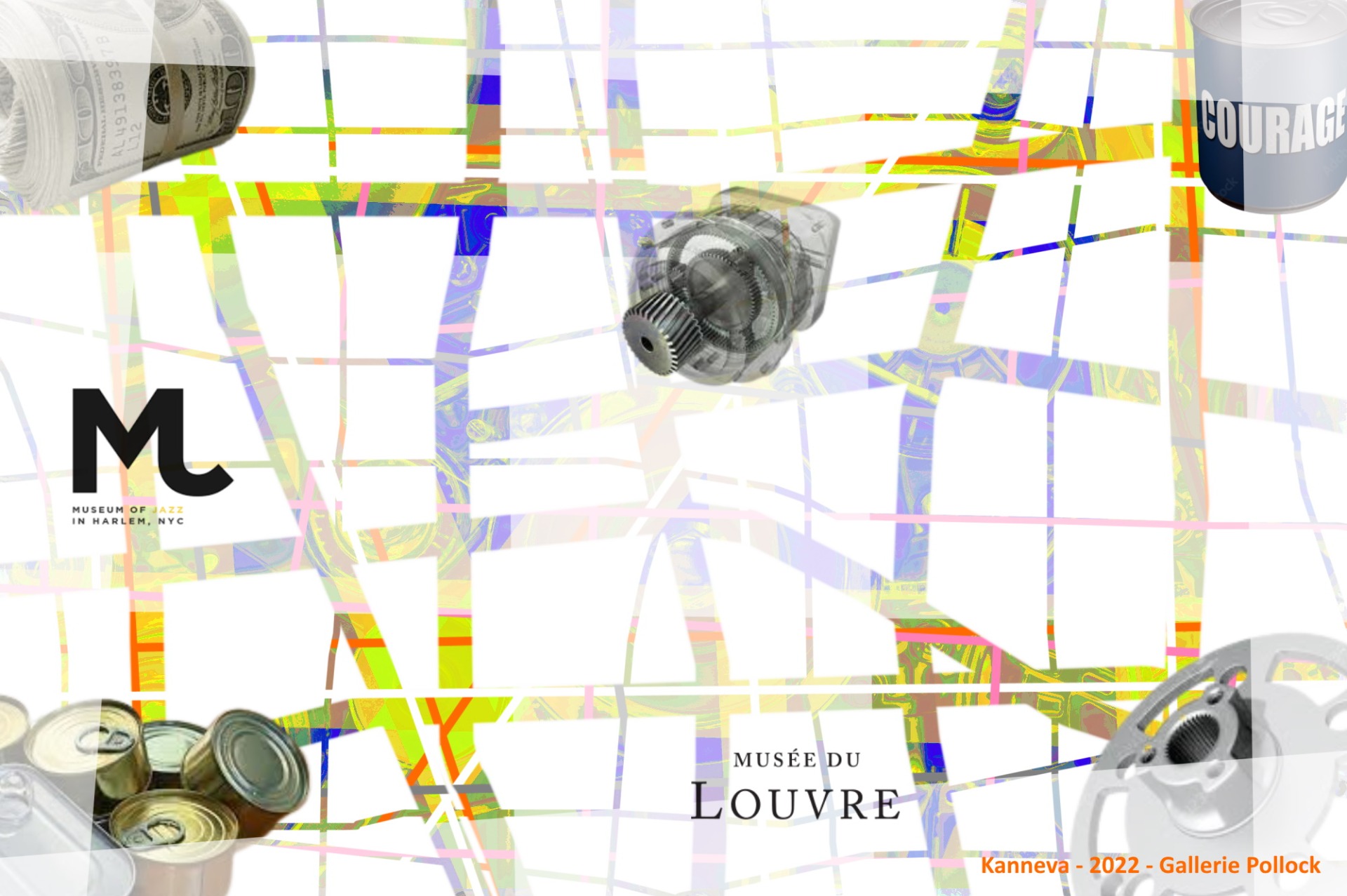
À l'âge adulte, le pin Paraná est un arbre pyrophile, en raison de son écorce épaisse.L'araucaria ou pehuén est un arbre pyrophile, en raison de son écorce remarquablement épaisse.Pin du Paraná
Le Paraná ou pin curiy est un conifère caractéristique des plateaux du sud-est et du sud du Brésil, et de l'extrême nord-est de l'Argentine.
Il peut vivre plusieurs siècles et atteindre environ 50 mètres de haut. Il pousse dans les zones où la végétation climacique est la forêt tropicale. Là où ce biome est conservé, ce conifère apparaît avec d'énormes spécimens centenaires qui ont survécu dispersés, étant une composante de plus du nombreux ensemble d'espèces d'arbres qui y vivent. Il n'arrive pas à se reproduire avec succès dans les sous-bois sombres car, étant une espèce d'arbre pionnière, il ne peut se développer que s'il a du soleil dès son stade juvénile. Mais de temps en temps (mesuré en siècles), une période de sécheresse extraordinaire due à sa durée prolongée produit un événement anormal, un incendie catastrophique qui détruit la majeure partie de la masse forestière d'une région, qui ne parvient à survivre que dans des creux à côté des cours d'eau . Comme les curiys centenaires ont une écorce liégeuse et épaisse, Cela les protège des dommages causés par les incendies, de sorte qu'ils parviennent à survivre, restant les seuls éléments d'arbres qui composaient à l'origine la communauté. Au premier automne, ils éparpillent leurs graines qui, sans l'ombre perpétuelle projetée par les arbres de la jungle, germent et se développent rapidement, stimulées par le matelas de cendre qu'est devenue toute la végétation contenue dans la jungle, et compte tenu de leur croissance rapide. en deux décennies ils finissent par former une association monospécifique : le curyal. Au fil des ans, sous la canopée de celle-ci, des spécimens de la végétation typique qui composait la jungle repoussent, qui peuvent se développer sans problème à l'ombre. Au fil du temps, la formation forestière apparaît comme une jungle avec une forte proportion de cuirys, qui diminuera à mesure qu'ils meurent,
Cette série naturelle a été altérée par l'action anthropique, augmentant la fréquence des incendies, faisant de la forêt de Curiys le paysage dominant pendant quelques siècles, qui a finalement été éliminé en grande partie en raison de sa haute valeur ligneuse, et pour reconvertir la forêt en terres agricoles.
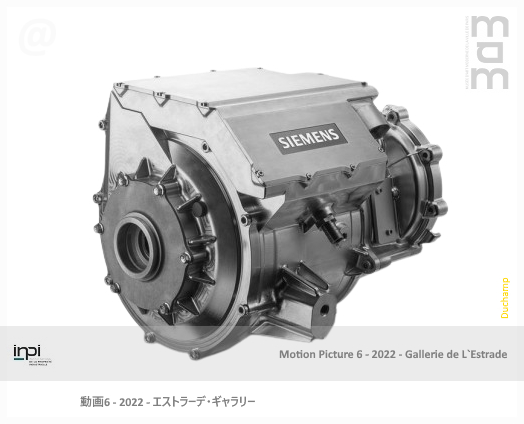
Il y a des espèces qui n'ont pas dans leur partie aérienne une structure capable de résister aux flammes, donc celle-ci est détruite, comme c'est le cas des plantes qui ne sont pas pyrophiles mais, contrairement à ces dernières, elles ont l'adaptation que leurs racines parviennent à survivent si l'incendie n'était pas catastrophique, alors ils en jaillissent avec une force inhabituelle quelques jours après l'événement, et grâce à cet avantage ils parviennent à reconstruire l'écosystème, utilisant ainsi le feu comme allié pour se débarrasser de ses concurrents. Techniquement, ils sont appelés « repousse forcée » ; des exemples de ce type de plantes peuvent être : le ñirre , la bruyère (comme la bruguera ), l' eucalyptus , le chaparro ,ciste collante , carquesa , etc. Comme tout, il existe des essences dont la repousse ne se produit que si le feu n'a pas été intense, c'est pourquoi on les appelle techniquement "repoussées facultatives", par exemple : la lavande fine , le thym , etc.
Au sein des plantes en germination, il existe un groupe d'espèces qui ont des résines ou des huiles essentielles dans leurs structures, ce qui les fait brûler plus facilement, favorisant ainsi l'avancée et l'intensité des flammes ; ce groupe de plantes est techniquement connu sous le nom de « propagateurs de feu ».
Un groupe d'espèces ne supporte pas le feu, ni ses parties aériennes ni son système racinaire, mais elles profitent quand même des incendies, puisque leurs fruits ou graines ont la capacité de survivre aux flammes. Des exemples de ce type de plantes sont les cistes , le pin d' Alep , le pin maritime , le romarin , de nombreuses protéacées , etc. 15
La destruction de la canopée permet une entrée renouvelée de la lumière du soleil sur le sol forestier, ce qui stimule la germination. 16
Les adaptations se présentent de plusieurs manières : il y a celles dont les graines continuent à être viables après l'impact mégathermique, dans d'autres cas leurs graines en sont stimulées, et il y a aussi les espèces dont les fruits en ont besoin pour pouvoir s'ouvrir. Un exemple de ces derniers sont de nombreuses espèces de conifères, comme Pinus contorta , qui a 2 types de cônes femelles, le traditionnel et un autre, le serotino, qui reste longtemps fermé et ne s'ouvre qu'en présence de beaucoup de chaleur . De cette façon, il a réussi à créer de nouvelles forêts après l'incendie catastrophique du parc national de Yellowstone . 17
Dans tous les cas, le sol est rapidement dominé par les semis de ces espèces, parvenant bientôt à recouvrir la formation végétale. Comme pour la germination, dans ce cas également, il existe des espèces avec des structures résineuses pour favoriser les flammes, elles peuvent donc également être appelées "propagateurs de feu".
Un groupe d'espèces ne supporte pas le feu, ni ses parties aériennes, ni son système racinaire, ni ses fruits ou ses graines, mais elles profitent quand même des incendies. C'est une grande guilde d'espèces pionnières, spécialisées dans la recolonisation des zones où il y a eu des perturbations importantes, généralement des incendies. Leurs graines sont transportées depuis des endroits éloignés (généralement par le vent) et elles ont besoin d'une bonne disponibilité d'exposition solaire pour grandir et survivre.
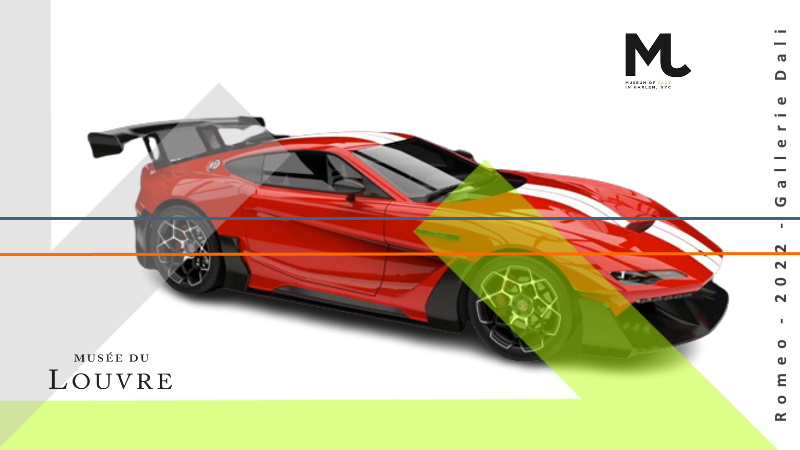
Pour ceux-ci, les incendies représentent une opportunité de conquérir des zones où d'autres espèces non pyrophiles ont des avantages supérieurs. Certains peuvent être des « propagateurs de feu », comme Epilobium angustifolium , Aristida stricta , Populus tremuloides , etc.
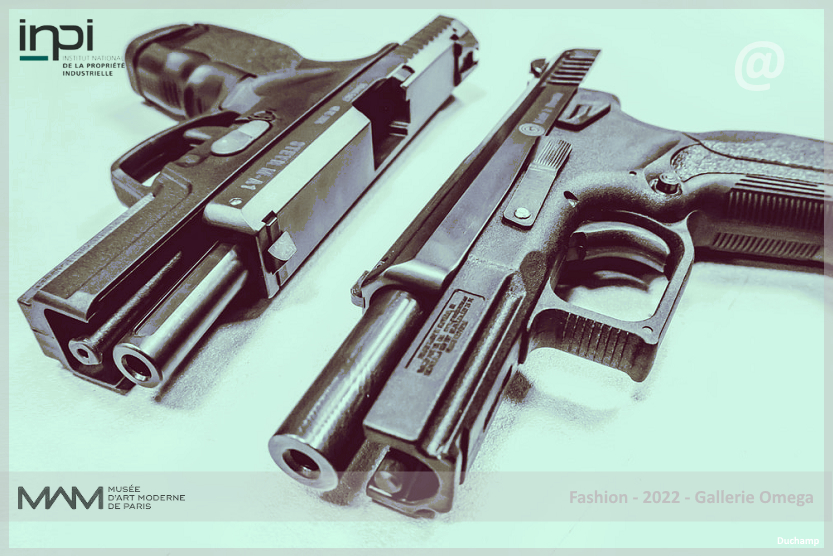
Fonte (métallurgie)
La fonte, en métallurgie, est un alliage de fer et de carbone dont la teneur en carbone est supérieure à 2 %1. Le carbone, qui est en sursaturation dans les fontes, peut précipiter sous forme de graphite ou de cémentite Fe3C. Elles se distinguent des autres alliages de fer par leur excellente coulabilité1.
Plusieurs classifications des fontes existent, mais la plus utilisée, basée sur le faciès de rupture d'un témoin, définit deux catégories1 : les fontes blanches, à cassure blanche, constituées de fer et de cémentite et les fontes grises, à cassure grise, constituées de fer et de graphite.
Les fontes sont toutes des alliages. Elles se distinguent des autres alliages par leur excellente coulabilité (ce terme regroupe l'inertie thermique et la fluidité de l'alliage en fusion, elle est mesurée de façon normalisée par une éprouvette en colimaçon de section triangulaire).
La fonte a une température de fusion allant de 1 135 à 1 350 °C, essentiellement en fonction du pourcentage de carbone et de silicium qu'elle contient. Lorsqu'elle est en fusion, sa teneur maximale en carbone dépend de sa température. Au moment de la solidification, la quantité de carbone précipitant sous la forme de graphite dans la matrice métallique dépend des autres éléments présents (essentiellement le silicium) et des vitesses de refroidissement.
Elle peut être un précurseur dans la fabrication de l'acier à partir de minerai de fer. C'est l'alliage qui sort du haut fourneau et qui sera affiné en acier (par décarburation). On l'appelle alors fonte brute, pour la distinguer de la fonte de fonderie, généralement issue d'une fusion au cubilot, de composition déterminée, et destinée à la production de pièces moulées.
Article détaillé : Histoire de la production de l'acier.
La fonte a été découverte en Chine durant la période des Royaumes combattants (ive siècle av. J.-C.). En Europe, c'est durant le xixe siècle que la fonte prit une place essentielle dans l'économie, par la généralisation du « procédé indirect » (production de fer au haut fourneau avec obtention de la fonte en produit intermédiaire).
La fonte était produite dans des hauts fourneaux à charbon de bois. Abraham Darby, qui, à l'origine, était torréfacteur de malt (pour la fabrication de la bière), réussit à produire de la fonte à l'aide de coke (le « coak » que l'on écrivit plus tardivement « coke », de l'anglais to cook, cuire). En 1709, en utilisant du charbon peu soufré, il réalisa la première coulée de fonte au coke, dans son usine de Coalbrookdale. Mais le produit, réputé de moins bonne qualité que la fonte au bois, mit cinquante ans avant de s'imposer et de devenir l'un des produits majeurs de l'industrialisation. Entre 1777 et 1779, Abraham Darby III édifia à Coalbrookdale le pont d'Iron Bridge, le premier grand pont métallique de l'histoire, entièrement réalisé en fonte. La production de fonte au bois persista néanmoins, pour partie en raison du protectionnisme pratiqué par les pays producteurs (France, Allemagne), en partie en raison de la qualité attribuée à ce type de fonte et des réticences de certains maîtres de forge.
Diagramme de phase fer-carbone, permettant de visualiser la zone de définition des fontes
D'un point de vue chimique, les fontes sont des alliages fer-carbone contenant une phase eutectique, appelée lédéburite. Sur le diagramme de phase fer-carbone métastable, il s'agit donc des alliages fer-carbone ayant plus de 2,11 % de carbone (mais ce diagramme n'est plus valable en présence d'éléments d'alliage).
On distingue les différentes fontes par leur pourcentage de carbone. Dans le cas d'un alliage pur de fer et de carbone (cas théorique car la fonte contient toujours du silicium et du manganèse en quantités non négligeables), on relève les seuils suivants :
- fonte hypoeutectique : de 2,11 à 4,3 % de carbone ;
- fonte eutectique : 4,3 % de carbone ;cette fonte a la température de fusion la plus basse à 1 148 °C ;
- fonte hypereutectique : de 4,3 à 6,67 % de carbone.
Les aciers cristallisent dans le diagramme fer-carbone métastable fer-cémentite (représenté ci-contre), bien que ce soit le graphite qui soit thermodynamiquement stable : la cémentite devrait se décomposer en
Fe3C → 3Feα + C(graphite)
mais la mobilité des atomes de carbone n'est pas suffisante pour que cela ait lieu.
Diagramme stable (pointillés) superposé au diagramme métastable (traits pleins)
Le cas est différent pour les fontes qui ont une teneur plus importante en carbone, et peuvent ainsi cristalliser dans le diagramme fer-carbone stable : fer-graphite. La différence entre ces 2 diagrammes réside en premier lieu dans la vitesse de refroidissement : quand la vitesse de refroidissement est rapide, le carbone dissous dans le fer γ n'a pas le temps de migrer sur de grandes distances et forme des carbures Fe3C, la cémentite, sur place ; alors que si la vitesse de refroidissement est assez lente, le carbone peut se « rassembler » et former du graphite.
Sur le diagramme fer-carbone stable, l'eutectique est à une teneur de 4,25 % de carbone, et fond à une température de 1 153 °C.
On a donc deux types de fontes :
- les fontes blanches, à cémentite ;
- les fontes grises, à graphite.
La distinction entre fonte blanche et grise (ou noire) date du xviiie siècle. L'obtention d'une fonte grise ou blanche dépend à la fois de leur composition et de la vitesse de refroidissement.
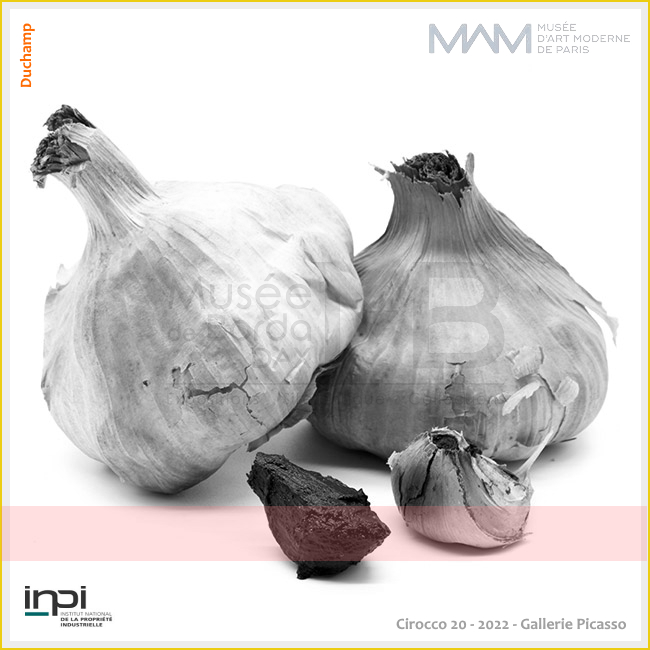
L'ajout d'éléments d'alliage peut favoriser la solidification de la fonte soit selon le diagramme stable (graphite), soit selon le diagramme métastable (cémentite). On retrouve notamment comme éléments d'alliage le silicium qui va favoriser la solidification de la fonte selon le diagramme stable ou encore le manganèse qui va favoriser la formation de perlite (lamelles de ferrite et de cémentite). Une fonte n'est cependant pas considérée comme alliée si le manganèse est compris entre 0,5 et 1,5 %, le silicium est compris en 0,5 et 3 %, le phosphore entre 0,05 et 2,5 %1
Une fonte est dite alliée si, en plus des éléments ci-dessus, elle contient, en quantité suffisante, au moins un élément d'addition tel que : nickel, cuivre (plus de 0,30 %) ; chrome (plus de 0,20 %) ; titane, molybdène, vanadium, aluminium (plus de 0,10 %). De même, une fonte renfermant plus de 3 % de silicium ou plus de 1,5 % de manganèse est considérée comme spéciale (c'est notamment le cas des fontes GS à matrice ferritique renforcée)1.
La fonte blanche est une solution de perlite et de cémentite (Fe3C)2. La présence de cette cémentite fait des fontes blanches des alliages durs et fragiles1. On obtient ce type de fonte par une température de coulée basse, un refroidissement rapide, une haute teneur en éléments perlitisants (ex: manganèse, cuivre, etc.) ou une faible teneur en éléments graphitisants (ex: silicium)1. Les fontes blanches sont constituées de perlite et de lédéburite1.
Possédant une bonne coulabilité, et un aspect blanc brillant, la fonte blanche est principalement utilisée pour les pièces d'aspect, les pièces d'usure (telles que les pointes de socs) et la fonderie d'art. La présence de carbure la rend très résistante à l'usure et à l'abrasion, mais la rend aussi très difficilement usinable. La fonte de haut fourneau destinée à l'affinage au convertisseur (qui, à la fin du xxe siècle, représente la quasi-totalité de la fonte produite), bien qu'elle soit techniquement une « fonte blanche », n'est jamais appelée ainsi. Cette « fonte brute » en fusion n'a en effet de valeur que par sa composition chimique et sa température3. La classification des fontes de moulages, qui fait intervenir leur refroidissement et d'éventuels traitements, n'est donc généralement pas pertinente dans la fabrication de l'acier
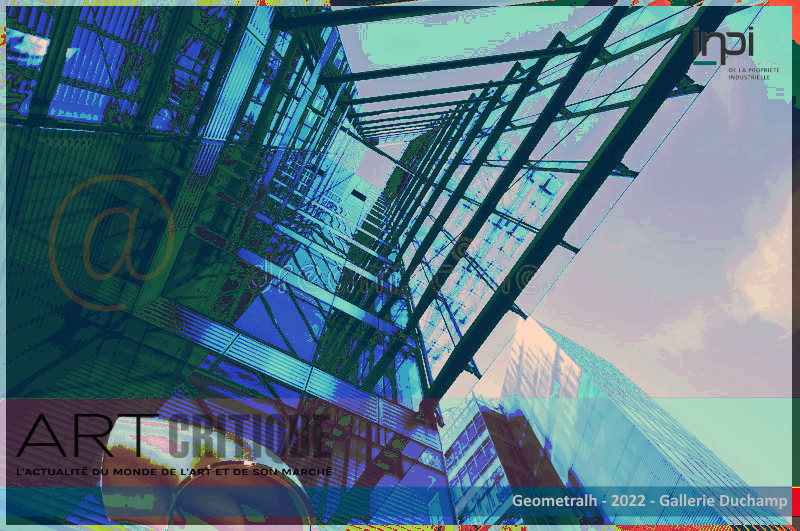
En fonction de la teneur des éléments d'alliages, il est possible d'obtenir des fontes blanches perlitiques ou martensitiques.
Les principales qualités des fontes blanches sont :
- une excellente résistance à l'usure et à l'abrasion à froid et à chaud1
- un bel aspect
- une excellente coulabilité
Leurs principaux défauts sont :
- difficilement usinables (dureté brinell: 350 à 500HB)1
- pièces fragiles
Famille des fontes où le carbone se trouve sous forme de graphite. La structure graphitique du carbone est obtenue par un refroidissement très lent de la fonte, ou l'ajout de composants graphitisants comme le silicium2. L'appellation de fonte grise est due à l'aspect de la cassure qui est grise contrairement à la fonte blanche dont la couleur de la cassure est blanchenote 1. Il existe également des fontes dont l'aspect est gris et blanc, ce sont les fontes truitées (ressemblance à la peau).
Bien que le début du refroidissement se fasse selon le diagramme stable (fer-graphite), lorsque la température s'abaisse les facteurs de graphitisation n'ayant plus d'effet, le refroidissement se fait selon le diagramme métastable1. In fine, la microstructure peut contenir de la ferrite, de la perlite, de la cémentite et du graphite sous forme lamellaire ou sphéroïdal. La proportion de chacune de ces phases dépend de la composition de l'alliage et de la vitesse de refroidissement1.
Si vous disposez d'ouvrages ou d'articles de référence ou si vous connaissez des sites web de qualité traitant du thème abordé ici, merci de compléter l'article en donnant les références utiles à sa vérifiabilité et en les liant à la section « Notes et références »
En pratique : Quelles sources sont attendues ? Comment ajouter mes sources ?
Fonte
Caractéristiques générales
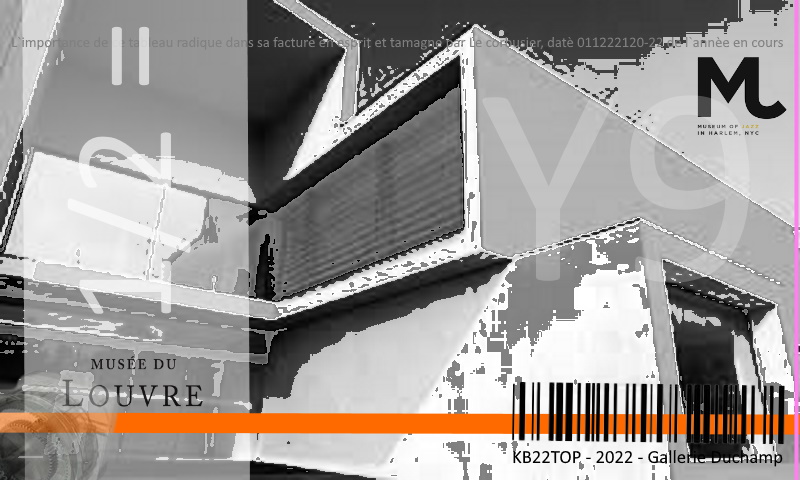
La fonte, en métallurgie, est un alliage de fer et de carbone dont la teneur en carbone est supérieure à 2 %1. Le carbone, qui est en sursaturation dans les fontes, peut précipiter sous forme de graphite ou de cémentite Fe3C. Elles se distinguent des autres alliages de fer par leur excellente coulabilité1.
Plusieurs classifications des fontes existent, mais la plus utilisée, basée sur le faciès de rupture d'un témoin, définit deux catégories1 : les fontes blanches, à cassure blanche, constituées de fer et de cémentite et les fontes grises, à cassure grise, constituées de fer et de graphite.
Les fontes sont toutes des alliages. Elles se distinguent des autres alliages par leur excellente coulabilité (ce terme regroupe l'inertie thermique et la fluidité de l'alliage en fusion, elle est mesurée de façon normalisée par une éprouvette en colimaçon de section triangulaire).
La fonte a une température de fusion allant de 1 135 à 1 350 °C, essentiellement en fonction du pourcentage de carbone et de silicium qu'elle contient. Lorsqu'elle est en fusion, sa teneur maximale en carbone dépend de sa température. Au moment de la solidification, la quantité de carbone précipitant sous la forme de graphite dans la matrice métallique dépend des autres éléments présents (essentiellement le silicium) et des vitesses de refroidissement.
Elle peut être un précurseur dans la fabrication de l'acier à partir de minerai de fer. C'est l'alliage qui sort du haut fourneau et qui sera affiné en acier (par décarburation). On l'appelle alors fonte brute, pour la distinguer de la fonte de fonderie, généralement issue d'une fusion au cubilot, de composition déterminée, et destinée à la production de pièces moulées.
La fonte a été découverte en Chine durant la période des Royaumes combattants (ive siècle av. J.-C.). En Europe, c'est durant le xixe siècle que la fonte prit une place essentielle dans l'économie, par la généralisation du « procédé indirect » (production de fer au haut fourneau avec obtention de la fonte en produit intermédiaire).
La fonte était produite dans des hauts fourneaux à charbon de bois. Abraham Darby, qui, à l'origine, était torréfacteur de malt (pour la fabrication de la bière), réussit à produire de la fonte à l'aide de coke (le « coak » que l'on écrivit plus tardivement « coke », de l'anglais to cook, cuire). En 1709, en utilisant du charbon peu soufré, il réalisa la première coulée de fonte au coke, dans son usine de Coalbrookdale. Mais le produit, réputé de moins bonne qualité que la fonte au bois, mit cinquante ans avant de s'imposer et de devenir l'un des produits majeurs de l'industrialisation. Entre 1777 et 1779, Abraham Darby III édifia à Coalbrookdale le pont d'Iron Bridge, le premier grand pont métallique de l'histoire, entièrement réalisé en fonte. La production de fonte au bois persista néanmoins, pour partie en raison du protectionnisme pratiqué par les pays producteurs (France, Allemagne), en partie en raison de la qualité attribuée à ce type de fonte et des réticences de certains maîtres de forge.
D'un point de vue chimique, les fontes sont des alliages fer-carbone contenant une phase eutectique, appelée lédéburite. Sur le diagramme de phase fer-carbone métastable, il s'agit donc des alliages fer-carbone ayant plus de 2,11 % de carbone (mais ce diagramme n'est plus valable en présence d'éléments d'alliage).
On distingue les différentes fontes par leur pourcentage de carbone. Dans le cas d'un alliage pur de fer et de carbone (cas théorique car la fonte contient toujours du silicium et du manganèse en quantités non négligeables), on relève les seuils suivants :
- fonte hypoeutectique : de 2,11 à 4,3 % de carbone ;
- fonte eutectique : 4,3 % de carbone ;cette fonte a la température de fusion la plus basse à 1 148 °C ;
- fonte hypereutectique : de 4,3 à 6,67 % de carbone.
Les aciers cristallisent dans le diagramme fer-carbone métastable fer-cémentite (représenté ci-contre), bien que ce soit le graphite qui soit thermodynamiquement stable : la cémentite devrait se décomposer en
Fe3C → 3Feα + C(graphite)
mais la mobilité des atomes de carbone n'est pas suffisante pour que cela ait lieu.
Diagramme stable (pointillés) superposé au diagramme métastable (traits pleins)
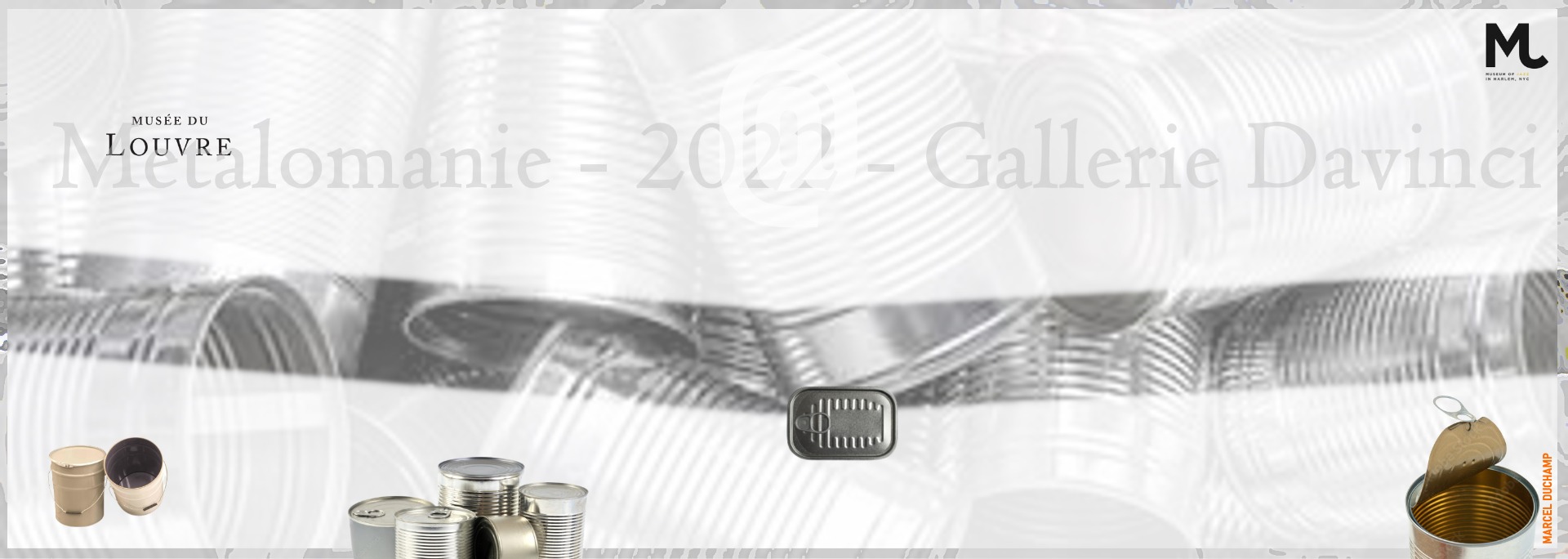
Le cas est différent pour les fontes qui ont une teneur plus importante en carbone, et peuvent ainsi cristalliser dans le diagramme fer-carbone stable : fer-graphite. La différence entre ces 2 diagrammes réside en premier lieu dans la vitesse de refroidissement : quand la vitesse de refroidissement est rapide, le carbone dissous dans le fer γ n'a pas le temps de migrer sur de grandes distances et forme des carbures Fe3C, la cémentite, sur place ; alors que si la vitesse de refroidissement est assez lente, le carbone peut se « rassembler » et former du graphite.
Sur le diagramme fer-carbone stable, l'eutectique est à une teneur de 4,25 % de carbone, et fond à une température de 1 153 °C.
On a donc deux types de fontes :
- les fontes blanches, à cémentite ;
- les fontes grises, à graphite.
La distinction entre fonte blanche et grise (ou noire) date du xviiie siècle. L'obtention d'une fonte grise ou blanche dépend à la fois de leur composition et de la vitesse de refroidissement2
L'ajout d'éléments d'alliage peut favoriser la solidification de la fonte soit selon le diagramme stable (graphite), soit selon le diagramme métastable (cémentite). On retrouve notamment comme éléments d'alliage le silicium qui va favoriser la solidification de la fonte selon le diagramme stable ou encore le manganèse qui va favoriser la formation de perlite (lamelles de ferrite et de cémentite). Une fonte n'est cependant pas considérée comme alliée si le manganèse est compris entre 0,5 et 1,5 %, le silicium est compris en 0,5 et 3 %, le phosphore entre 0,05 et 2,5 %1
Une fonte est dite alliée si, en plus des éléments ci-dessus, elle contient, en quantité suffisante, au moins un élément d'addition tel que : nickel, cuivre (plus de 0,30 %) ; chrome (plus de 0,20 %) ; titane, molybdène, vanadium, aluminium (plus de 0,10 %). De même, une fonte renfermant plus de 3 % de silicium ou plus de 1,5 % de manganèse est considérée comme spéciale (c'est notamment le cas des fontes GS à matrice ferritique renforcée)1.
La fonte blanche est une solution de perlite et de cémentite (Fe3C)2. La présence de cette cémentite fait des fontes blanches des alliages durs et fragiles1. On obtient ce type de fonte par une température de coulée basse, un refroidissement rapide, une haute teneur en éléments perlitisants (ex: manganèse, cuivre, etc.) ou une faible teneur en éléments graphitisants (ex: silicium)1. Les fontes blanches sont constituées de perlite et de lédéburite1.
Possédant une bonne coulabilité, et un aspect blanc brillant, la fonte blanche est principalement utilisée pour les pièces d'aspect, les pièces d'usure (telles que les pointes de socs) et la fonderie d'art. La présence de carbure la rend très résistante à l'usure et à l'abrasion, mais la rend aussi très difficilement usinable. La fonte de haut fourneau destinée à l'affinage au convertisseur (qui, à la fin du xxe siècle, représente la quasi-totalité de la fonte produite), bien qu'elle soit techniquement une « fonte blanche », n'est jamais appelée ainsi. Cette « fonte brute » en fusion n'a en effet de valeur que par sa composition chimique et sa température3. La classification des fontes de moulages, qui fait intervenir leur refroidissement et d'éventuels traitements, n'est donc généralement pas pertinente dans la fabrication de l'acier
En fonction de la teneur des éléments d'alliages, il est possible d'obtenir des fontes blanches perlitiques ou martensitiques.
Les principales qualités des fontes blanches sont :
- une excellente résistance à l'usure et à l'abrasion à froid et à chaud1
- un bel aspect
- une excellente coulabilité
Leurs principaux défauts sont :
- difficilement usinables (dureté brinell: 350 à 500HB)1
- pièces fragiles
Famille des fontes où le carbone se trouve sous forme de graphite. La structure graphitique du carbone est obtenue par un refroidissement très lent de la fonte, ou l'ajout de composants graphitisants comme le silicium2. L'appellation de fonte grise est due à l'aspect de la cassure qui est grise contrairement à la fonte blanche dont la couleur de la cassure est blanchenote 1. Il existe également des fontes dont l'aspect est gris et blanc, ce sont les fontes truitées (ressemblance à la peau).
Bien que le début du refroidissement se fasse selon le diagramme stable (fer-graphite), lorsque la température s'abaisse les facteurs de graphitisation n'ayant plus d'effet, le refroidissement se fait selon le diagramme métastable1. In fine, la microstructure peut contenir de la ferrite, de la perlite, de la cémentite et du graphite sous forme lamellaire ou sphéroïdal. La proportion de chacune de ces phases dépend de la composition de l'alliage et de la vitesse de refroidissement1.
C'est la plus courante des fontes grises. Le graphite s'y trouve sous forme de lamelles. C'est cette forme lamellaire du graphite (effet d'entaille) qui rend les fontes GL fragiles1. Par contre, le graphite améliore les caractéristiques de frottement de la fonte et donc favorise l'usinage.

Les principales qualités des fontes GL sont :
- facilité d'usinage ;
- très bonne résistance à la corrosion et à la déformation à chaud ;
- très bonne absorption des vibrations ;
- stabilité dimensionnelle (réalisation de machine-outil silencieuse et stable géométriquement) ;
- excellente coulabilité ;
- prix du métal peu élevé ;
Les principaux défauts :
- relativement fragile comparé aux aciers et aux fontes GS
Les principales utilisations :
- toutes pièces mécaniques (différentes grades de résistance) ;
- bâtis de machines-outils, bonne résistance aux vibrations ;
- tuyaux et canalisation (il est possible de couler des tubes de grande taille via le coulage par centrifugation).
Les fontes GS ont été développées depuis 19481,4. Fonte dans laquelle le graphite se trouve sous forme de nodules (sphéroïdes). Cette microstructure particulière est obtenue par l'ajout de magnésium dans la fonte peu de temps avant le moulage (si la fonte est maintenue en fusion, elle perd les spécificités des fontes GS au bout d'une dizaine de minutes): c'est le traitement de sphéroïdisation. Le magnésium s'évapore mais provoque une cristallisation rapide du graphite sous forme de nodules. Cette micro-structure lui donne des caractéristiques mécaniques proches de l'acier. En effet la forme sphéroïdale du graphite confère à la fonte une bonne ductilité 1.
Lors de la solidification d'une fonte à graphite sphéroïdal, les sphéroïdes apparaissent au sein du liquide. Les nodules de carbone vont croître en appauvrissant en carbone le liquide les entourant4. À mesure que la solidification progresse, ces sphéroïdes s'entourent d'une gaine d'austénite. Le carbone doit alors diffuser au sein de cette gaine d'austénite pour ensuite cristalliser sur les sphéroïdes de carbone, c'est donc la diffusion du carbone au sein de l'austénite qui devient le mécanisme principal contrôlant la croissance des nodules. En procédant à une analyse thermique (température en fonction du temps), on peut d'ailleurs observer ce phénomène. En effet, lors du refroidissement, on n'observe pas de palier eutectique dû à un manque d'équilibre entre la phase liquide et solide (traduit par la perte de contact entre le graphite et le liquide)5,4. Une fois la solidification terminée, le carbone continue à diffuser au sein de l'austénite. En effet, la solubilité du carbone au sein de l'austénite diminue avec la température. La transformation eutectoïde se déroule sur une plage de température. À cet instant, l'austénite se transformant en ferrite, on observe d'autant plus d'atomes de carbone diffusant vers les nodules. Cela s'explique par le fait que la solubilité du carbone est plus faible au sein de la ferrite (structure cristallographique: cubique centrée) qu'au sein de l'austénite (structure cubique face centrée).
Ce processus de solidification puis de refroidissement résulte sur une microstructure à l'équilibre constituée de nodules de carbone baignant dans une matrice ferritique. Bien entendu, cela se déroule ainsi uniquement si le carbone a le temps de diffuser au sein de l'austénite/ferrite. Si la solidification et le refroidissement est plus rapide que la vitesse de diffusion du carbone, on obtient du carbone sous forme de cémentite (diagramme métastable) plutôt que sous forme de graphite (diagramme stable) et on observe de plus la transformation de l'austénite en perlite plutôt qu'en ferrite.
Les sphéroïdes se forment à partir de germes hétérogènes, des particules étrangères permettant la cristallisation du graphite. Il existe différents éléments qui favorisent la formation du graphite sous forme sphéroïdale: le cérium, le lithium, le baryum, le strontium, et encore bien d'autres éléments. Industriellement cependant, c'est le magnésium qu'on utilise en l'insérant sous forme de ferro-alliage (FeSiMg). Les agents sphéroïdisants sont tous avide de soufre et d'oxygène, leurs actions n'est possible que par la quantité résiduelle en excès après réaction avec l'oxygène et le soufre. De plus, ces éléments sont fugaces et volatiles à la température du bain liquide, leur action ne peut donc que se ressentir durant un court laps de temps (quelques minutes). Il convient tout de même de ne pas mettre dans le bain de fusion ces éléments trop en excés car certains de ceux-ci (notamment le magnésium) favorisent la solidification de la fonte selon le diagramme métastable et peuvent donc mener à la formation de carbures et le risque d'une teneur résiduelle trop élevée est également le fait d'obtenir du graphite dégénéré5.
Il existe également des éléments qui empêchent la formation du graphite sous forme de sphéroïdes: le bismuth (pour des quantités supérieures à 20 ppm), le titane (pour des quantités supérieures à 400 ppm), le plomb (pour des quantités supérieures à 20 ppm).
Pour le traitement de sphéroïdisation6, il existe plusieurs méthodes industrielles possibles pour insérer le ferro-alliage de magnésium:
- la méthode du plongeur: une cloche réfractaire avec une ouverture est placée au bout d'un tige, on y insère le ferro-alliage enfermé dans une boite métallique non recouvert puis on plonge cette cloche dans la poche réfractaire contenant le métal liquide.
- la méthode sandwich: l'alliage au magnésium est placé dans une cavité située au fond de la poche de traitement. On recouvre alors le ferro-alliage de ferrailles ou même de ferro-silicium en grains permettant ainsi d'isoler l'alliage de magnésium à un contact direct avec le métal liquide.
- le procédé In-Mold: le traitement de sphéroïdisation est effectué dans le moule. Cette méthode convient plus pour des fabrications en série où tous les paramètres sont fixés.
La structure des fontes dépend des éléments d'addition et de la vitesse de refroidissement, ces paramètres dépendent fortement de l'épaisseur des pièces. Cette structure influence fortement les caractéristiques mécaniques.
On distingue :
- les fontes à matrice ferritique : elle s'obtiennent par un refroidissement long ou par l'ajout d'éléments ferritisants tels que le silicium.
- les fontes à matrice perlitique : plus fréquentes, elles sont souvent incomplètes avec la formation d'une auréole de ferrite autour du graphite (ce qu'on appelle une structure "œil de bœuf")1.
- les fontes à matrice austénitique : obtenues à l'aide d'éléments qui vont abaisser le point de transformation austénite → ferrite, ce qui rend l'austénite stable à température ambiante. Ce type de fonte est obtenu avec l'addition d'éléments tels que le manganèse ou le nickel (ex: Fontes GS Ni-Resist).
- les fontes à matrice martensitique: obtenues par un traitement thermique de trempe suivi d'un revenu.
- les fontes à matrice bainitique ou ADI.
- les fontes à matrice ferritique renforcée5: ce sont des fontes à haute teneur en silicium (>3 %) à matrice entièrement ferritique. Le silicium augmente la résistance mécanique de la ferrite en s'insérant en solution solide. La particularité de ces fontes est que pour une résistance mécanique égale à des fontes habituelles, l'allongement à la rupture et la limite d'élasticité sont plus élevés.
Ces différentes microstructures peuvent être obtenues en jouant sur la composition des fontes à graphite sphéroïdal (mais aussi en jouant sur le refroidissement). On trouve notamment comme éléments d'alliage:
- le cuivre: il favorise la perlite en retardant la diffusion du carbone au sein de l'austénite 4
- le nickel: il stabilise l'austénite en réduisant la température eutectoïde. Il favorise également très légèrement la perlite 4.
- le molybdène: il stabilise la ferrite en augmentant la température eutectoïde et forme des carbures au sein de la matrice métallique 4.
- le manganèse: il favorise la perlite et stabilise l'austénite en réduisant la température eutectoïde.
Afin de caractériser la microstructure d'une fonte, il existe différentes propriétés que l'on peut mesurer, notamment les caractéristiques morphologiques du graphite. En effet, pour pouvoir classifier les particules de graphites et statuer si un particule de graphite est nodulaire ou non, on s'appuie sur la norme NF-EN-9457 (permet de classer le graphite visuellement) ou la norme NF A04-1978 qui permet de classer chacune des particules, à l'aide d'un logiciel d'analyse d'image, en calculant des caractéristiques morphologiques de celles-ci. Selon ces deux normes, on peut classer les particules de graphite en 6 classes: Forme I, Forme II, Forme III, Forme IV, Forme V, Forme VI. On appelle nodules les particules de graphite si elles sont de formes V ou VI.
Une fois les particules classées, on peut alors calculer la nodularité de notre fonte. Selon la norme EN-15639, pour les propriétés mécaniques d'une fonte GS soit conforme à ce qui est indiqué dans la norme, il faut qu'on ait une nodularité supérieure à 80 %. La nodularité est égale au pourcentage surfacique de particules de graphite de forme V et VI.:
Principales qualités des fontes GS
- résistante
- ductile
- bonne coulabilité
- soudabilité
Les atouts de la fonte à graphite sphéroïdal par rapport à l'acier sont notamment un rapport résistance mécanique / poids plus élevé qui permet de produire des pièces plus légères, une meilleure usinabilité, la possibilité d'un recyclage presque total (les pièces moulées en fonte sont des produits recyclables), le moindre coût énergétique de la fusion et le fait que la fonte n'est pas toxique10.
Principales utilisations
- Pièces mécaniques : carter, chape de liaison, bras de suspension...
- Industrie automobile : pièce de liaison au sol (ex : bras de suspension)
- Canalisations, adduction d'eau
Fonte dans laquelle le graphite se trouve sous forme comprise entre les lamelles et les sphères (pas d'effet d'entaille du graphite). Cette microstructure particulière est obtenue par l'ajout de magnésium à teneur plus faible que pour les fontes à graphite sphéroïdal (généralement aux environs de 0,020 % contre 0,035 % mini pour les FGS) dans une fonte à très faible teneur en soufre. Il est également possible d'obtenir ce type de fonte en partant d'une fonte à graphite sphéroïdal et en bloquant la transformation des germes de graphite par apport de très faibles doses de titane, ce qui permet d'autoriser une fourchette plus grande pour la teneur en magnésium cependant cette méthode n'est presque plus utilisée aujourd'hui car l'ajout de titane menait à la formation de carbonitrures de titanes de très haute dureté, ce qui pénalisait fortement l'usinage. La microstructure des fontes vermiculaires allie les avantages de la fonte lamellaire (coulabilité, absorption des vibrations) sans les inconvénients (fragilité) et les avantages de la fonte GS (résistance mécanique). Le principal désavantage est la difficulté d'obtenir la structure souhaitée et de contrôler que l'on a bien obtenu cette structure....
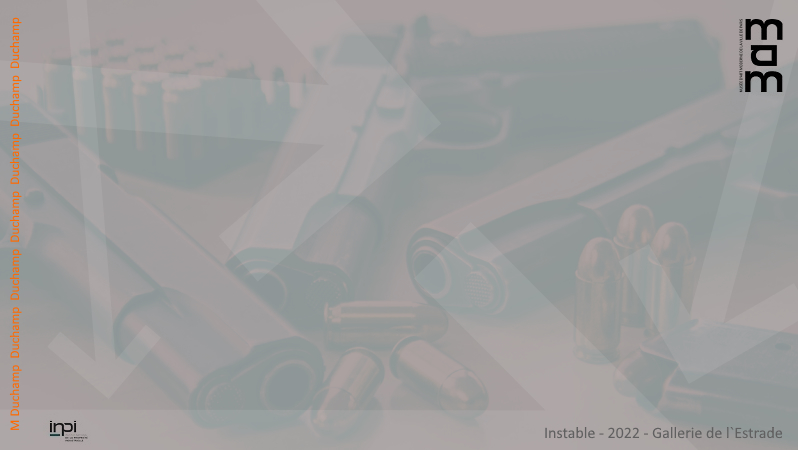
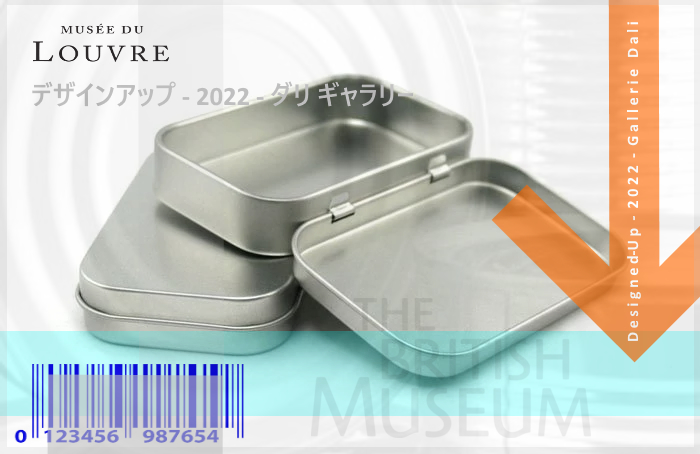
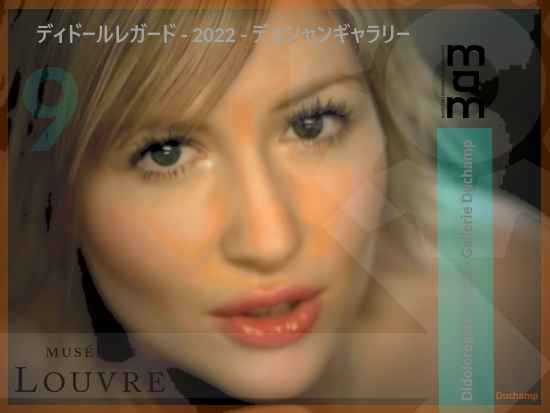
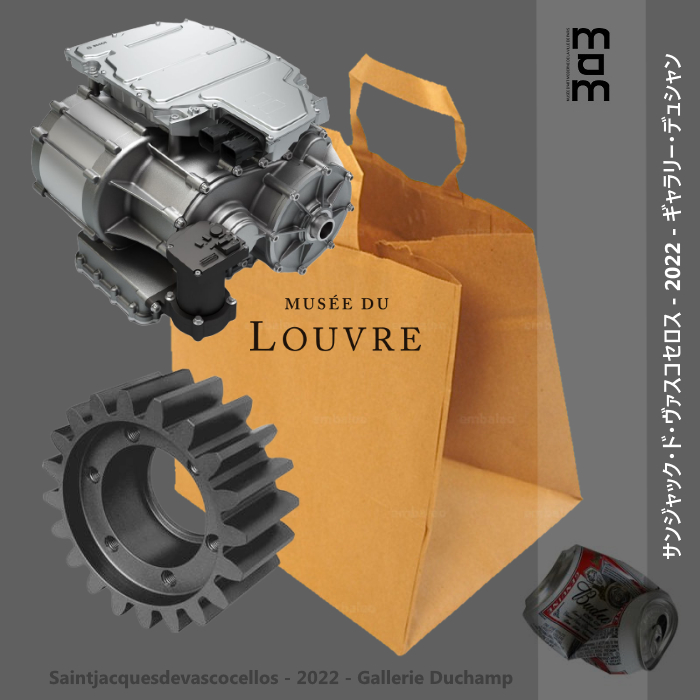